射出成形のサイクルタイムを最適化するには?成形条件と金型設計の視点から解説
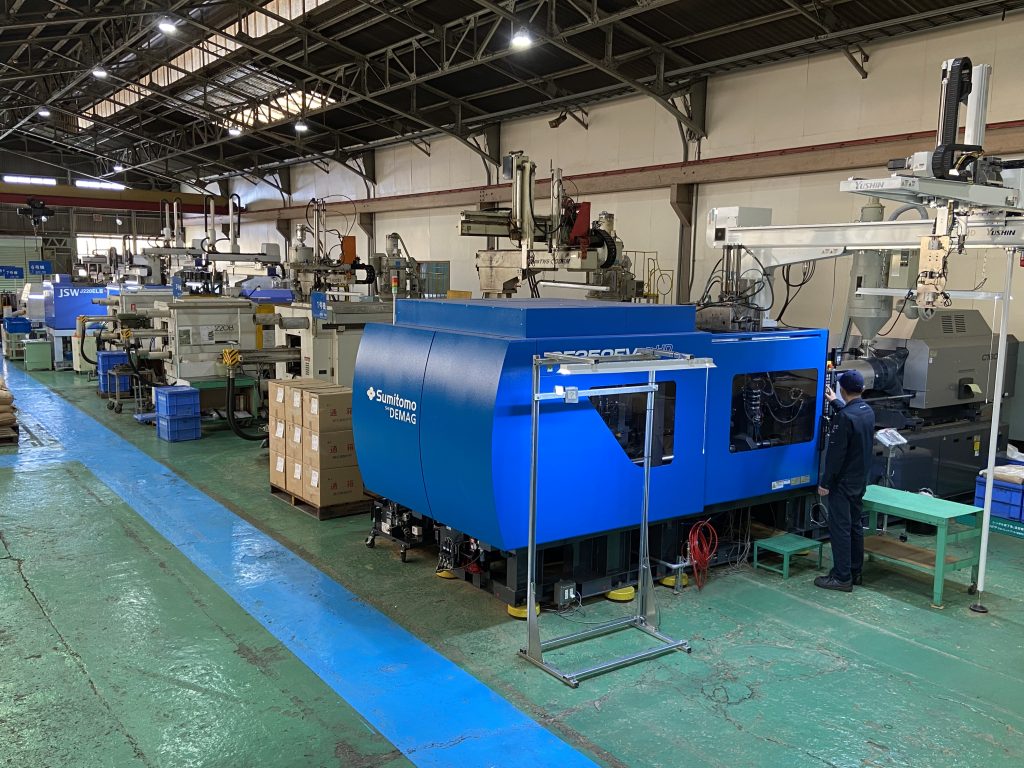
射出成形において「サイクルタイム」は、生産効率やコスト構造に直結する最重要指標です。わずか1秒の差が、月間数千個・数万個の生産に影響を与えることも珍しくありません。本記事では、サイクルタイムを構成する各工程の基本から、なぜ時間がかかるのかという要因分析、さらに日東電気が行っている改善アプローチまで、まとめて解説いたします!
射出成形におけるサイクルタイムとは?
射出成形における「サイクルタイム」とは、1ショットあたりの成形サイクル、つまり金型を閉じてから次のショットを開始するまでにかかる一連の工程時間を指します。成形工場においては、生産効率・コスト構造・品質管理のいずれにおいても、サイクルタイムは最も重要なKPI(重要業績評価指標)の一つです。そんなサイクルタイムは以下のような工程で構成されます。
サイクルタイムを構成する主な工程
サイクルタイムは以下のような6工程に分けられ、それぞれが全体の時間と品質に密接に関わっています
- 型閉じ(クランプ)
成形機の可動側と固定側の金型が高い圧力で密着し、射出準備を整える工程です。 - 射出充填(インジェクション)
スクリューで加熱・可塑化された樹脂を金型内へ高速で充填します。流動性・圧力制御が重要です。 - 保圧(パック)
樹脂の収縮を抑え、寸法安定性を高めるために、所定の圧力を一定時間維持します。過不足は不良の原因になります。 - 冷却
樹脂が金型内で固化するまでの工程です。サイクルの中でも最も時間を要しやすく、冷却効率の設計が重要です。 - 型開き(オープン)
成形品を取り出すために金型を開きます。安全装置やセンサーとの連携がポイントになります。 - 取り出し・計量準備
成形品をエジェクタやロボットで排出し、次ショットに向けて樹脂の可塑化・計量を同時に進行します。
これら全体が1つの成形サイクルであり、その合計時間が「サイクルタイム」となります。
なぜサイクルタイムが重要視されるのか?
サイクルタイムは、単に「早ければ良い」というものではなく、「短縮しながらも品質を担保する」ことが求められます。その理由は以下の通りです。
- 生産性の最大化
1時間あたりに成形できるショット数が増えるため、同一設備での生産能力が向上します。 - 製造コストの低減
成形時間に比例して発生する設備償却・人件費・電力などのランニングコストを低減できます。 - 短納期対応力の向上
サイクルが速ければ、受注から出荷までのリードタイムを圧縮でき、顧客満足度の向上につながります。 - 現場改善の評価軸として有効
定量的な数値として改善成果を測定でき、PDCAサイクルをまわす指標としても優れています。
射出成形のサイクルタイムが長くなる主な要因とは?
射出成形においてサイクルタイムは、製品1ショットあたりの成形に要する時間全体を指しますが、これがわずか1秒長くなるだけでも、日産・月産単位では大きな損失につながります。したがって、「なぜこの時間がかかっているのか?」という原因分析を工程ごとに行い、構造的に改善していく必要がございます。
ここでは、サイクルタイムを構成する代表的な工程ごとに「時間が延びてしまう主要因」を整理し、課題解決の糸口を探ります。
冷却時間が過剰になっている
冷却工程は、成形サイクルの中でも最も時間を要する領域です。特に生産性の高い製品群では、冷却時間がサイクル全体の50%以上を占めることもあります。
- 冷却回路の深さや配置が最適化されていない
- 金型材質の熱伝導性が低い(一般構造用鋼やS50Cなど)
- 配管設計が直列化され、冷却ムラが生じている
- スケールやサビによって冷却水の流速が低下している
上記のような要因により、必要以上の冷却時間を設定せざるを得ない状況が発生する可能性がございます。
型開閉動作が遅い
型開き・型閉じの動作は、一般的に自動制御されているため、軽視されがちな領域ですが、実際には下記のような原因で数秒単位の遅延が発生しています。
- クランプ速度設定が保守的で、動作に余裕を持たせすぎている
- 金型重量やサイズに対して装置仕様が過剰または不足している
- ガイドピンや摺動部の摩耗によるスムーズな動作の妨げ
- 安全装置の過剰なセンサー感度による停止ロス
これらは積み重ねで1〜2秒、設備や条件によっては5秒以上のサイクルロスにつながるケースもあります。改善の第一歩は、「なぜこの速度なのか?」「この制御設定は最適か?」という問いをもつことです。
取出し動作の手間やタイミングのズレ
取り出し工程は、自動化が進む一方で、設定ミスや設備老朽化によって非効率が蓄積しやすい領域です。
- ロボットアームの動作速度が最大限活用されていない
- ワークの離型性が悪く、取り出しに時間がかかる
- 型からの製品残りや、ズレによるワーク脱落トラブル
- 取出しセンサーの応答遅れや異常停止によるサイクルロス
特に「ワークが金型内に残る」といった現象は、オペレーターの再確認・手動排出の手間など、サイクル外の隠れたコストにもなるため、早急な対応が求められます。
成形条件が最適化されていない
- 保圧時間が長すぎて冷却と重複してしまっている
- 可塑化時間の余裕設定が過剰
- ショートショットを恐れるあまり、過度に低速で射出している
成形条件は、品質を守るための最重要項目ですが、逆に言えば「不具合が出ていなければそのままにされやすい」側面があります。より早いサイクルタイムで安定した成形をするためには、金型や製品の仕様を確認の上、成形条件を最適化する必要がございます。
設備・金型の老朽化やメンテナンス不足
- バルブ、油圧系統、センサーなどの応答性低下
- 金型冷却穴の詰まりや腐食
- スライド部の潤滑不良やガイドピンのガタつき
これらはサイクルそのものをじわじわと蝕む“見えにくい敵”です。例えば金型内部のスケール蓄積によって冷却効率が10%落ちた場合、冷却時間は数秒単位で延びます。こういった見えない部分にこそ、時間短縮の可能性が潜んでいます。
日東電気ならではのサイクルタイム最適化
射出成形におけるサイクルタイム短縮は、単なる条件設定の見直しだけでは不十分です。金型の設計思想、成形条件の最適化、そして現場での改善活動まで、トータルに対応できる体制が求められます。その中で日東電気では、金型製作から成形、改善提案までを一貫して対応できる体制を構築しており、サイクルタイム短縮を実現しています。
金型設計から成形条件を見据えた最適な設計を提案
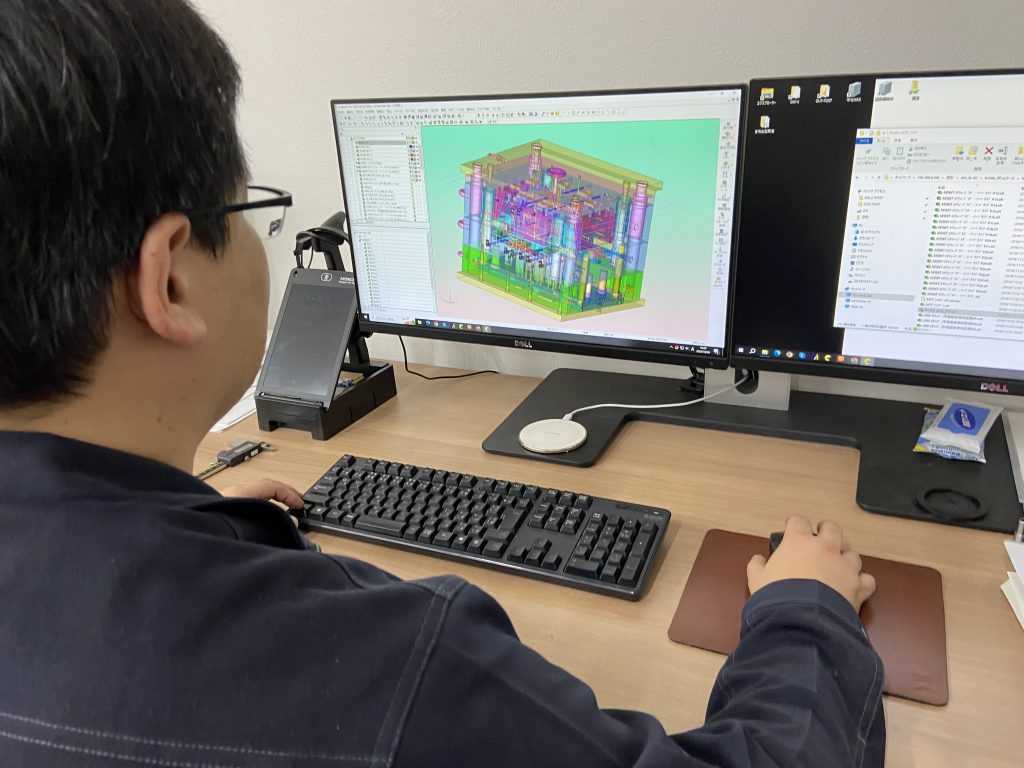
日東電気では、金型の設計段階から「成形性・サイクルタイム・メンテナンス性」を意識した設計を行っています。
- 冷却回路の流路設計を樹脂収縮や厚肉部位にあわせて最適化
- 型開閉構造におけるストローク・動作性の検証
- 設備仕様と連動したエジェクタ構造や金型重量の配慮
このように、単なる「形を作る金型」ではなく、「工程全体の効率性を考えた金型」を設計思想の基盤とすることで、設計の段階からサイクル短縮の下地を築いています。
支給金型にも対応、検証のうえで条件最適化を実施
日東電気では、自社で製作した金型だけでなく、顧客からの支給金型についても成形性やメンテナンス性を評価したうえで、サイクルタイム改善の提案を行っています。支給された金型の構造を内部確認し、冷却効率や摩耗状況を評価したり、現場の成形条件と突き合わせて、理想の射出圧力・冷却時間を設定しております。
ラック式金型によるサイクルタイム短縮
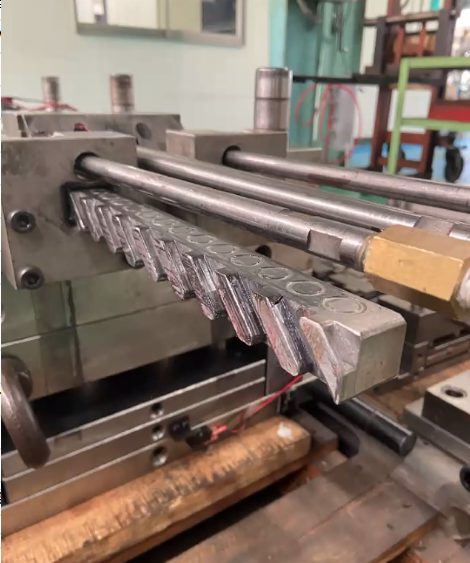
ストロークが長い射出成形で使用する金型において、サイクルタイムを向上させたい場合や金型・製品への負荷を軽減したい場合、油漏れのリスクや配線・メンテナンスの手間を軽減したい場合はラック式の金型がお勧めです。
>>ストロークが長い射出成形のサイクルタイムを短縮!?ラック式金型について解説します!
OEM・EMSパートナーズ.comを運営する日東電気はラック式金型の設計製作に対応しております。
また、万が一トラブルが発生した際も、迅速に対応することができます。自社内での修理・メンテナンス体制が整っているため、定期的なメンテナンスや製品形状が変更になった場合においても、短納期且つ低コストで製品のご提供を可能にしております。
定期的なメンテナンスを通じて金型の寿命を延ばし、安定した生産をサポートします。お客様に安心して製品をお任せいただけるよう、万全のサポート体制を提供しています。
日東電気ならではのプラスチック成形
金型設計~成形作業までの一貫対応
OEM・EMSパートナーズ.comを運営する当社は、プラスチック成形にも豊富な実績がございます。また、当社ではお客様からプラスチック成形のご依頼をいただいた際は、金型の設計・製作から行い、製品の量産までを一貫して対応しております。そのため、定期的なメンテナンスや製品形状が変更になった場合においても、同じ工場内での金型改造などの対応が可能となっているため、短納期且つ低コストで製品のご提供を可能にしております。
インサート成形・アウトサート成形にも対応
当社では様々な業界向けのプラスチック成形品に対応ができるよう、異種材料を組み合わせる必要がある場合や、高い強度や特殊な機能を要求される製品の製造に適しているインサート成形や、立型射出成形機を使い,金型内で金属プレートに金属などの部品を配置して一体成形するアウトサート成形も実施しております。
豊富な実績によるVA/VE提案
当社はプラスチック成形品について豊富な実績を有していることに加えて、常に最新のトレンドや情報を取り入れて製品を成形しております。そのため、お客様から製品データをいただいた際に起こりうる成形不良をリストアップし、事前に改善案を落とし込むことで、お客様にとって最適な成形の条件を対案いたします。
ワンストップ対応が実現する、高精度なエンプラ成形
OEM・EMSパートナーズ.comを運営する当社では、エンジニアリングプラスチックの成形にも対応しております。エンプラ成形は、ガスが発生しやすく、また金型やスクリューの摩耗が激しくなり、汎用プラスチックと比較して成形が困難とされています。
しかし当社では、材料特性を考慮した金型設計を行い、さらに射出成形機についても耐摩耗性スクリューを全成形機に搭載しており、ガラス繊維などの強化剤が含まれたエンプラでも問題なく量産成形が可能です
金型設計から製作、成形までワンストップ対応している当社だからこそ実現可能なのが、高精度エンプラ成形です。
プラスチック金型のことなら、OEM・EMSパートナーズ.comまで!
当サイトを運営する日東電気グループでは、金型設計製作からプラスチック成形・精密機械加工までをワンストップで対応しております。お客様のパートナー企業として様々な角度から技術提案をいたします。さらに当社では、部品の調達からアセンブリの工程管理まで、すべて請け負いますので、お客様の調達・管理コストの低減にも努めます。
プラスチック金型のことでお困りの方は、OEM・EMSパートナーズ.comまでご相談ください。
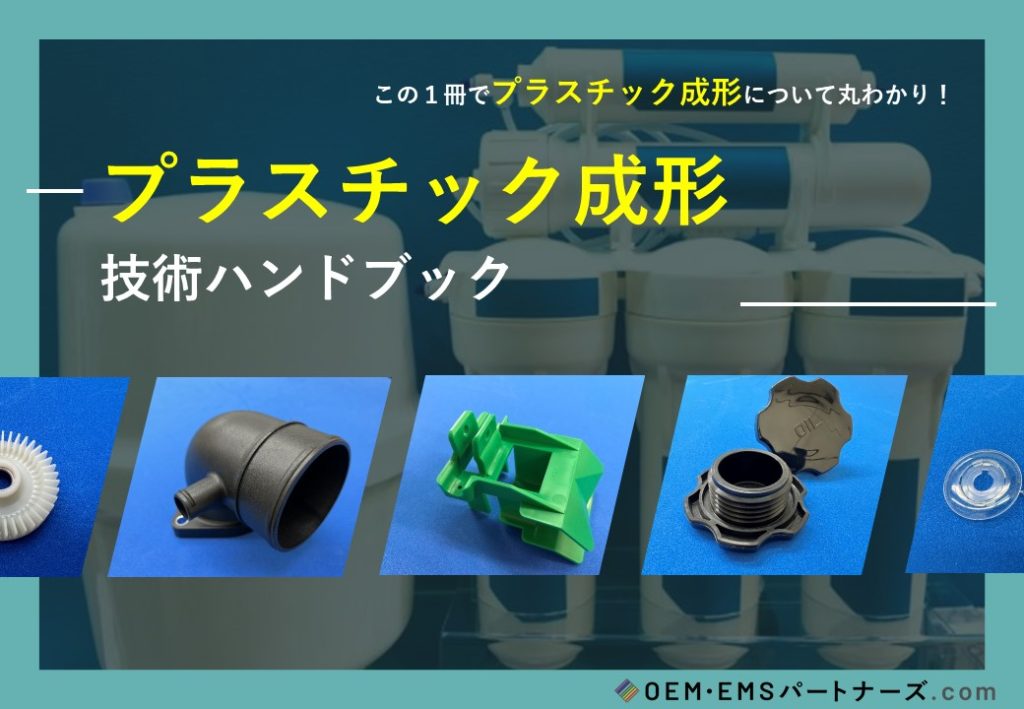
プラスチック成形・金型に関するよくある質問
ホットランナーの射出成形金型を検討していますが、イニシャルコストを抑えたいです。なにかいい方法はありますか?
ホットランナーの射出成形金型を検討していますが、イニシャルコストを抑えたいです。なにかいい方法はありますか?
ホットランナーとコールドランナーはどのように使い分けていますでしょうか?
特殊な樹脂材料なのですが、プラスチック成形はお願いできますか?
関連した基礎知識
-
インサート成形とは?複数部品を一体で成形するポイントを解説します!
製造業の効率化や高品質化が求められる中、インサート成形が注目を集めています。これは金属などのインサート部品をあらかじめ金型内にセットし、プラスチックを射出して一体成形する技術です。従来は接着剤やネジに...- 金型
- プラスチック成形
2025年3月11日
-
ストロークが長い射出成形のサイクルタイムを短縮!?ラック式金型について解説します!
射出成形において、生産性とコストを左右する重要な要素、それがサイクルタイムです。特に、型開きのストロークが100mmを超えてくるような形状の製品を成形する射出成形では、型開きの動作に時間がかかり、サイ...- 金型
- プラスチック成形
2024年12月11日