センタレス研削加工とは?原理からメリット・デメリットまで解説!
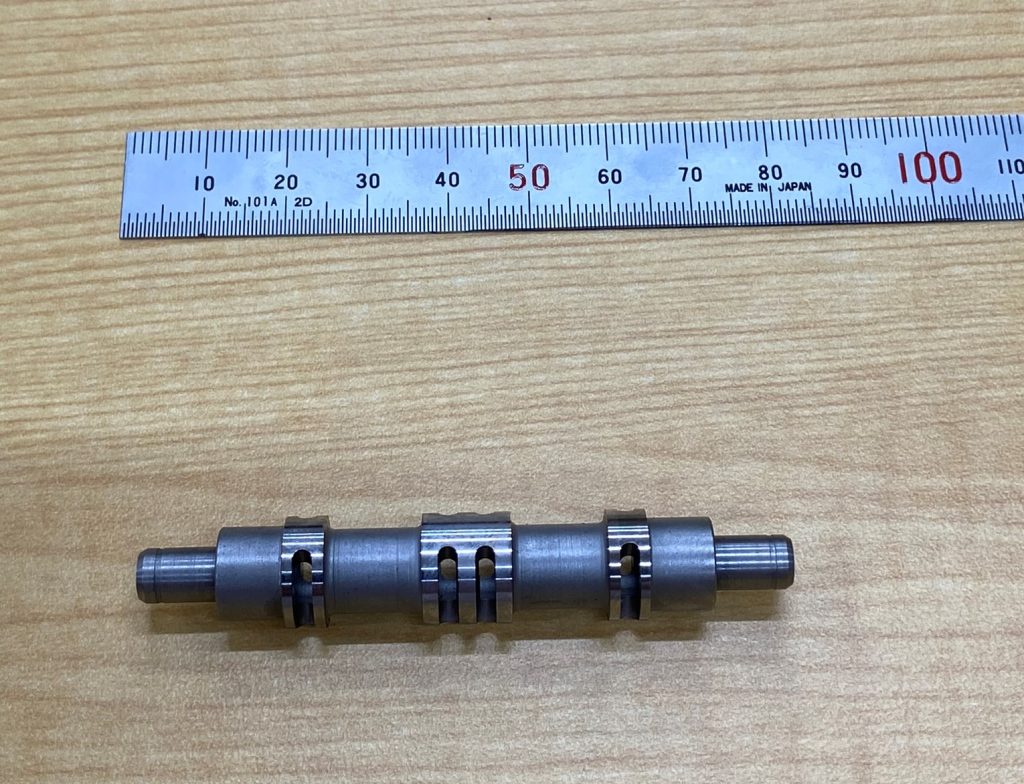
センタレス研削加工は、円筒形状のワークを、高速回転する研削砥石、ブレード、調整砥石(調整車、レギュレーターホイール)の3点で支持することでワークの外周を研削する加工方法です。センタレス研削加工にはいくつか種類がありますが、円筒研削とは違ってセンタ穴を必要とせず、固定されたブレードと調整砥石、研削砥石で素材を支持して研削加工を行います。そのため、素材の両端を固定する必要がなく、長尺の素材でもたわみの影響が少なく安定した精度を保てます。
ここでは、センタレス研削加工の概要から、センタレス研削加工の原理や造円作用、センタレス研削加工の種類、円筒研削との違い、メリット・デメリットから、当サイトを運営する日東電気ならではのセンタレス研削加工、そして実際に製作したセンタレス研削加工の製品事例まで、まとめてご紹介いたします。
センタレス研削加工とは?
センタレス研削加工とは、円筒状のワークの外側を滑らかに加工する技術で、ワークの真ん中に穴を開ける必要がない研削加工の方法です。センタレス研削加工では、円筒形状のワークを、高速回転する研削砥石、ブレード、調整砥石(調整車、レギュレーターホイール)の3点で支持することでワークの外周を研削します。
またセンタレス研削加工は、様々な言い方があります。英語では”Centerless grinder”と言いますが、日本語では「センターレス研削」「センタレス加工」「センタレス研磨」「センタレスグラインド」「心なし研削」「心無し研削」「芯なし研削」「無心研削」など、非常に多くの言い方があります。これらはすべてほぼ同義になりますが、研削盤メーカーの呼称等によって異なると考えられます。
センタレス研削加工の原理と、造円作用
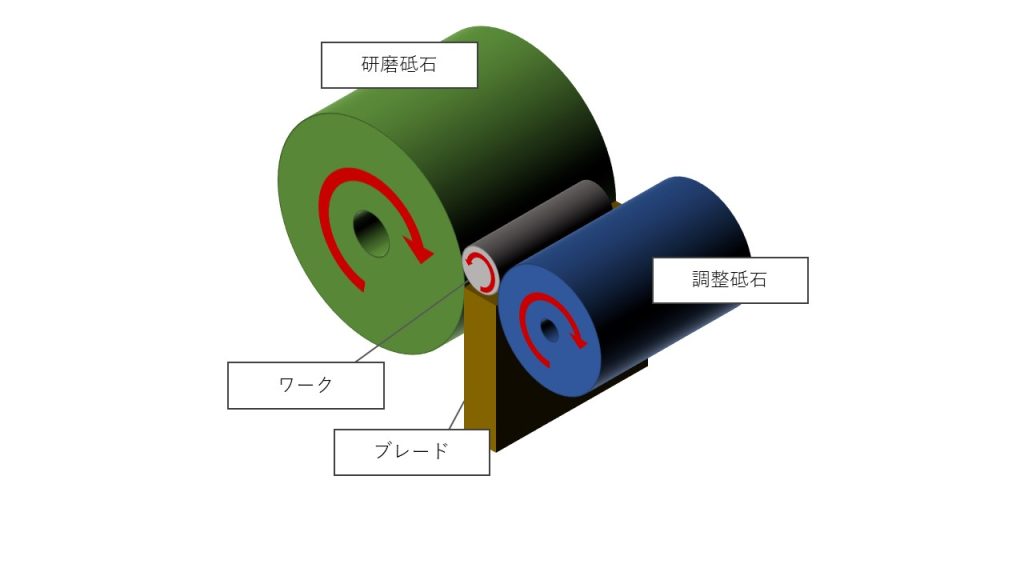
センタレス研削の原理・メカニズムは、2つの砥石による摩擦力にあります。ワークが研削砥石の回転に合わせて回ろうとしますが、研削砥石の反対側にある調整砥石が研削砥石と同じ方向に回転することで摩擦力が発生し、この摩擦力によって制動されます。そしてブレードによって支持されながら、低速回転する調整砥石の周速と同じスピードで回転しながら研削加工されます。この3点支持によりワーク全体が固定されるため、長尺物でもたわみが少なく、高精度な研削が可能です。
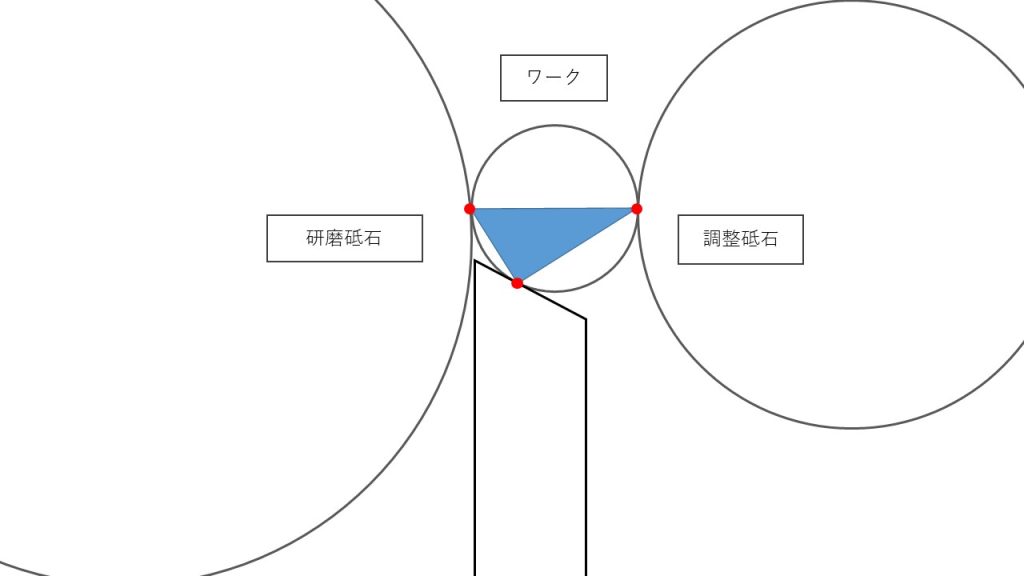
通常の研削では、ワークの中央に穴を開け、チャックで固定して研削加工をしますが、センタレス研削ではその工程が不要です。この技術は、「一直線上にない3点を円周とする円はただ一つだけ存在する」という定理を応用しています。そのため、円筒研削や旋盤のように中心を支持せずにワークの外周を加工することができます。
センタレス研削では、ワークの外周面が研削砥石、ブレード、調整砥石の3点で接しており、この3点を通る円はただ一つです。最初は形状に歪みのあるワークも、回転とともに歪みが一定の割合で研削され、小さくなっていきます。最終的には真円に近づくこの作用を「造円作用」と呼びます。
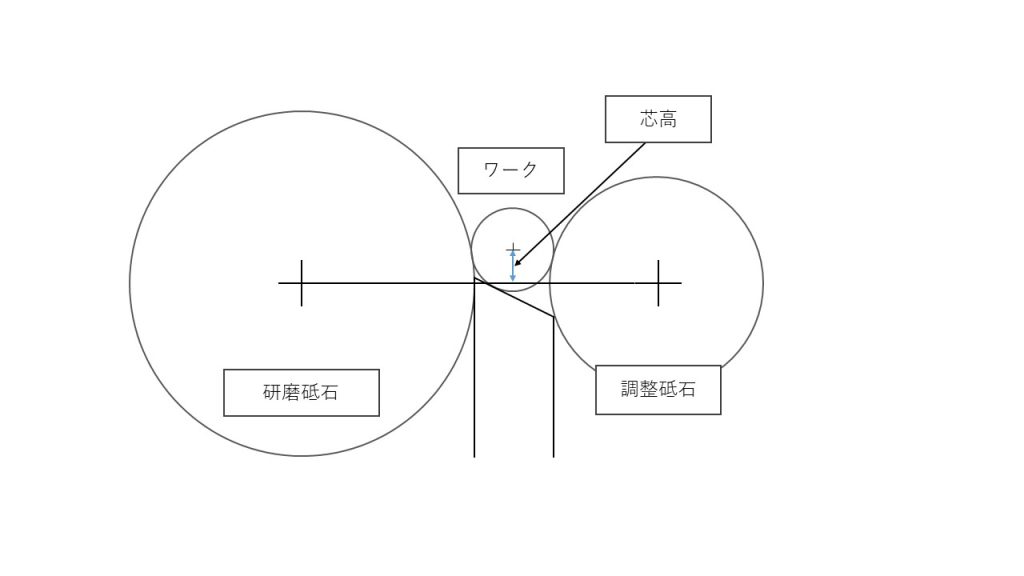
研削砥石と調整砥石の中心を結ぶ線とワークの中心の距離を「芯高」と呼びます。この芯高が適切でないと、真円度が不良になるため注意が必要です。例えば、芯高が高すぎる場合、ワークは「花びら形状」になり、逆に芯高が低すぎる場合、ワークは「おむすび形状」になってしまいます。
造円作用では、ブレードに置かれたワークが研削砥石と調整砥石の回転とともに少しずつ削られて形が整います。いびつな形のワークも、2つの砥石とブレードの接地する面を一定の速さで保ちながら回転させることで形が整い、繰り返し何度も接触させると歪みが少なくなり、最終的にはきれいな丸い形の円になります。
このようにして、センタレス研削では高精度な真円度を実現し、大量生産においても均一な品質を保つことができます。芯高の管理をしっかりと行うことで、安定した品質の製品を提供することが可能となります。
センタレス研削盤とは?
センタレス研削盤とは、センタレス研削加工をするための工作機械です。先ほどの通り、研削砥石、ブレード、調整砥石の3点が研削加工自体においては重要な要素を占めますが、各メーカーが高精度な加工ができるように、様々な工夫をセンタレス研削盤に施しています。
他サイトでは混同して表現されていることも多いですが、当サイトでは切り分けて「センタレス研削加工」と「センタレス研削盤」として記載していきます。
センタレス研削加工の種類
センタレス研削加工には、大きくスルーフィード研削(通し研削)とインフィード研削(停止研削)という2つの加工方法があります。
方法①:スルーフィード研削(通し研削)
スルーフィード研削は、ワークを砥石間に連続的に通しながら加工する研削方法です。調整砥石(調整車)の軸を一定の角度(1~4°)に傾けることで、ワークがブレード上を通過しながら研削加工が進みます。砥石の回転速度や角度が大きいほどワークは速く送られ、効率的に研削が行えます。特に長く続くリング形状のワークや段差やツバのないワークの大量生産に適しています。
方法②:インフィード研削(停止研削)
インフィード研削は、ワークを研削砥石と調整砥石の間に配置し、ワークの奥側にストッパーを設置して回転を止めることで行う研削方法です。インフィード研削ではワークを砥石の間に1つずつ出し入れして研削加工を行います。ワークに合わせて砥石形状を変更させることができるため、インフィード研削は段差やツバのあるワークや複雑な形状を持つワークに適しています。
センタレス研削と円筒研削との違いとは?
センタレス研削と円筒研削はどちらも高速回転する砥石を使用して素材を研削する技術ですが、その決定的な違いは素材の固定方法です。
円筒研削は、素材の外周を研削する方法の一つで、主軸台と心押し台で素材の両端を固定し、高速回転する砥石で削ります。円筒研削は、素材の形状や寸法を精密に加工するのに優れています。
一方でセンタレス研削は、センタ穴を必要とせず、固定されたブレードと調整砥石、研削砥石で素材を支持する研削方法です。このため、素材の両端を固定する必要がなく、長尺の素材でもたわみの影響が少なく安定した精度を保てます。
このように、円筒研削では主軸台と心押し台を用いて素材の両端をセンタ支持するのに対し、センタレス研削はブレード、研削砥石、調整砥石の3点で素材を支持します。センタレス研削はセッティング工程におけるメリットが大きく、量産性に優れている加工方法と言えます。また長尺物についてもたわみの影響を受けにくく、センタレス研削の方が安定して精度高く加工することができます。一方で、特に寸法精度や円筒度が必要な場合や、太くて重量があるものはセンタレス研削では加工が困難となり、円筒研削が選択されることが多いです。
りんごの皮むきに例えるのであれば、皮むき器に刺してリンゴを回しながら皮をむくのが円筒研削で、手で回しながら包丁で皮をむくのがセンタレス研削です。
センタレス研削加工のメリット
センタレス研削加工は、他の研削加工と比較しても、多くのメリットがあります。
メリット①:たわみの影響が少ない
センタレス研削加工は、ワーク全体をブレードと研削砥石、調整砥石の3点で支えるため、研削抵抗によるたわみの影響が少ないことが特徴です。このため、長尺の円筒や非常に小さなピンに対しても安定した研削加工が可能です。また、ワークを研削盤に取り付ける手間がないため、取り付け時の誤差がなく、研削精度を一定に保つことができます。
メリット②:センター穴の加工が不要
センタレス研削加工では、ワークの両端を支える必要がないため、センター穴の加工が不要です。円筒研削盤では、ワークを両端で支持するためにセンター穴を加工する必要がありますが、センタレス研削加工ではその工程が不要なため、工程の短縮が可能です。中心位置は砥石の回転によりワークを押し出すことで自然に出すことができます。
メリット③:連続生産による高い量産性
センタレス研削加工は、ワークを研削砥石と調整砥石で挟み、回転させながら研削するため、ワークの取り付けや排出作業が簡単に行えます。そのため、連続して生産が可能であり、加工時間を大幅に短縮できます。同じ大きさのワークを大量に加工することができるため、生産性の向上も見込めます。さらに、手間がかからず量産できることで作業効率が上がり、コストダウンにもつながります。
とくにスルーフィード研削の場合は、自動供給装置等と組み合わせることで、さらに量産対応をすることができます。
メリット④:段付きやR形状等の形状も加工が可能
センタレス研削加工は、ワークの形状に合わせて砥石を成形することで、段付きやR形状など幅広い加工が可能です。特にインフィード研削では、1回の研削で複雑な形状の加工が可能です。これにより、各種ピン類やパイプ、細長いワイヤーなどの加工が容易に行えます。一般的には円筒研削でしか対応できないと思われている段付きシャフトなども、実はセンタレス研削加工で加工することができます。
センタレス研削加工のデメリット・注意点
一方でセンタレス研削加工にはデメリットもあります。
精度は円筒研削にやや劣る
円筒研削ではワークをチャックしながら加工するため、マイクロレベルの高い表面性状や寸法公差を出すことができます。センタレス研削加工ではどうしても円筒研削と比較するとやや精度には劣ってしまいます。
重量があり、太径になると、対応が困難
機械の構造上、太くて重量があるものはセンタレス研削加工では加工が困難となり、円筒研削が選択されることが多いです。
キズや砥石の破損
センタレス研削加工では、キズや砥石の破損に注意が必要です。キズは、砥石がワークに合っていない場合や古くなった場合に発生します。また、砥石の破損によりワークにキズがつくこともあります。対策として、研削砥石の粒度を調整し、砥石自体を交換する必要があります。
びびりの発生
研削の際に砥石とワークに大きな負担がかかると、びびりが生じます。びびりとは、加工中に発生する振動の総称です。びびりの影響で加工精度が下がり、生産性も低下します。びびりを減らすためには、速度を遅くしたり、送り量を調整したりすることが重要です。
外周面の溝などの影響
センタレス研削加工は外周面を基準とするため、ワーク素材の外周面の溝や穴、真円度の影響を受けやすいです。
日東電気ならではのセンタレス研削
当サイトを運営する日東電気では、これまでに数多くのセンタレス研削加工を行ってまいりました。日東電気だからこそ可能なセンタレス研削加工としては、下記のような特徴があげられます。
真円度0.002以内を実現する高精度センタレス研削加工
当社のセンタレス研削加工では、通常は円筒研削の範疇である真円度0.002という高精度な加工についても、センタレス研削加工にて対応しております。
また従来は研磨加工を協力会社にて対応しておりましたが、現在は社内で公差0.002に収める研磨加工が可能となりました。
センタレス研削加工用のブレードを、平面研削を社内でメンテナンス対応
センタレス研削加工では、砥石の精度も重要ですが、見落とされがちなのがワークを支えるブレードです。このブレードの精度が悪いまま使用し続けると、もちろんこれもビビりや公差が悪くなる原因になります。しかし円筒研削を行う会社では平面研削盤を所有していないケースが多く、ブレードのメンテナンスも困難なため、そのまま使い続けているという場合も多くあります。
しかし日東電気では、センタレス研削加工用のブレードについても、社内にて平面研削盤を保有しているため、定期的に精度が高くなるようにメンテナンスを行っています。これが当社が高い継続精度でセンタレス研削加工を実現できている理由の1つです。
ロウ付け内製化
センタレス研削が必要となるシャフト等の丸物部品には、ロウ付け等の前後工程が必要になるケースが多くなります。当社では、ロウ付けや各種表面処理工程についても、内製化しつつ協力会社のネットワークを活用することで、すべて一貫対応しております。
図面には見えない嵌合部に関する設計フィードバック
シャフトやスプール、軸等の丸物部品は、相手部品が基本的には存在する嵌合部品です。そのため、図面で指定されているh公差よりもシビアな調整が必要になるケースも多々あります。部品メーカーとしては図面通りに作っているものの、メーカーからすると嵌めあいが悪く使えなければ意味がありません。
当社では、このような図面には指定がない嵌合部分に関する設計フィードバックも行っております。ただ図面通りに作るのではなく、その背景や用途を踏まえたうえで、最適なセンタレス研削による仕上げ加工を行います。
センタレス研削加工の単品少量・短納期対応
センタレス研削加工は通常量産にて使用される加工方法のため、単品少量での取り回しには向きづらい加工方法とされています。しかし当サイトを運営する日東電気では、センタレス研削加工の単品少量生産にも対応しております。大企業やセンタレス研削加工等の円筒研削加工を専門で行っている部品メーカーでは対応しないような、小回りが利くセンタレス研削加工によって、お客様に短納期にて対応することができます。
段付き形状へのセンタレス研削加工
多段付きのような段付き形状は、特殊な砥石や治具を使用することでセンタレス研削加工でも対応することができます。当社でも段付きシャフトのような丸物部品のセンタレス研削加工の実績もございますので、安心してお任せいただけます。
精密機械部品の調達力・在庫力・対応力
センタレス研削加工や精密機械加工以外にも、当社ではメーカー様の調達代行という側面も持っており、お客様に代わって各種部品の自社調達も行っております。
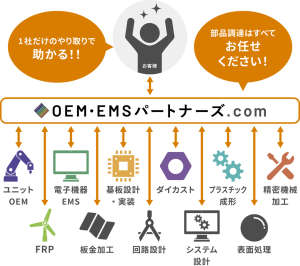
>>日東電気グループは、OEM・EMSのベストパートナーです。
センタレス研削に関する製品事例
続いて、実際に当社が製作したセンタレス研削・精密機械加工に関する製品事例をご紹介いたします。
スプール
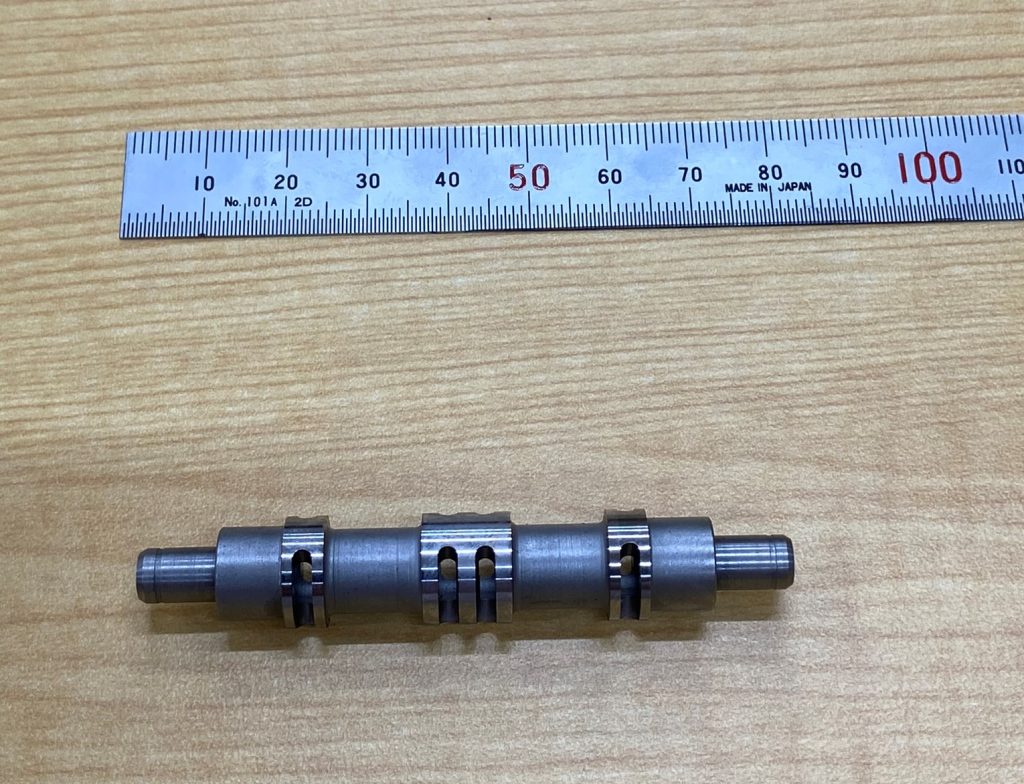
従来から取引のあるお客様から、油圧バルブ用部品の加工のご相談をいただきました。
該当する加工は長さがMAX110mm~MIN70mm、径φ10mm~φ18mmまでと範囲が広く、また形状に関しても40~50種の類似形状があったため、加工条件の選定に課題が多くございました。
当社では旋盤加工の為に専用バイトを製作して加工を実施。 また、検査工程においては始めに形状の確認・交差部の測定をすることで、同類形状の区分けをいたしました。
その後、各類似形状で共通使用ができる専用治具を設計・製作をすることで、類似形状ごとで加工条件を共通化し、オペレーションの最適化をすることでお客様に大変ご満足いただきました。
駆動軸
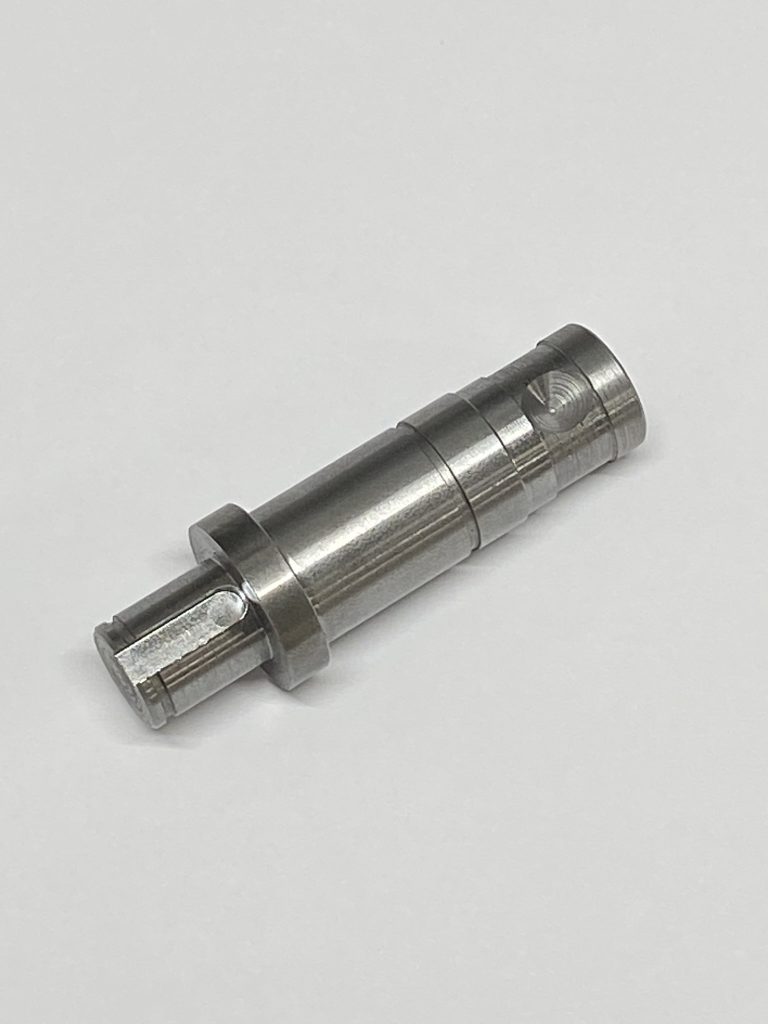
従来から取引のあるお客様から農機具部品の精密機械加工に関するご相談をいただきました。
ご相談をいただいた部品は加工精度が高く、コスト面でもお客様のご予算に納めるのが非常に厳しい状況でした。
そのため、通常ではNC旋盤加工・マシニング加工と複数工程で行う工程を、複合旋盤での対応を提案を行いました。
また、径方向にはめ合い公差h7が設定されていましたので、量産加工ではリングゲージを用い全数検査を行い、高精度の維持を実現しました。
また、キー溝部につきましてもブロックゲージによる全数検査にて対応しています。 本事例ではお客様のご要望であった高精度・低コストの双方を実現したことで、大変ご満足いただきました。
チェーンテンショナー
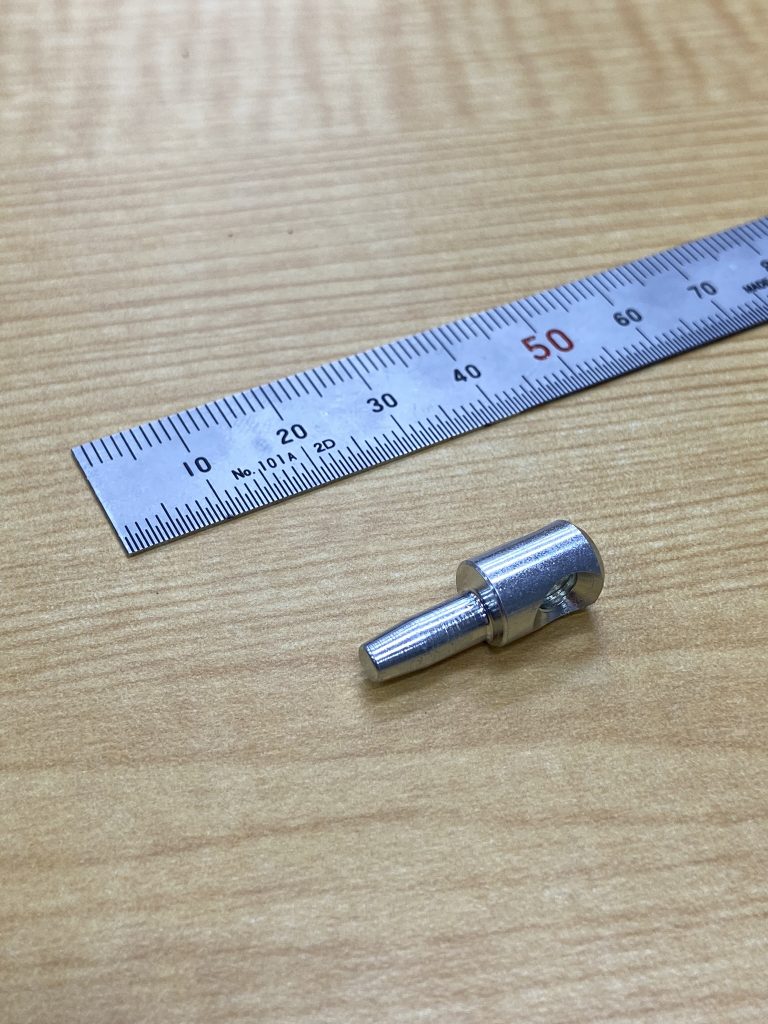
従来から取引のあるお客様から、チェーンソーのテンショナー部品の加工のご相談をいただきました。
該当部品は偏心形状であったため、偏心チャックを使用する非常に難度の高い加工でした。 また、側面にタップ加工が必要なために、旋盤加工後の自動タップ盤には専用治具を設計・製作して対応いたしました。
精密機械加工のことなら、OEM・EMSパートナーズ.comまで!
当サイトを運営する日東電気グループでは、精密機械部品の切削加工から最終の研磨工程までを一貫して行い、高精度な精密切削部品を数多く生産しています。当社では、アルミや銅の粘り気のある材質から、焼入れ材料の硬度の高いものまで豊富な加工実績がございます。また、航空機に使用されるタービンブレードのような大型の部品から、200mm以内の小型の部品までの加工可能サイズの範囲も広く、量産加工での精度は±100分の3mmと高精度での加工が可能です。
また機械加工については、単品小ロットの多品種少量生産における短納期を強みとしており、年間に数百種類の製品を製作しております。多くの部品加工業が取り回しを困難とするような製品について、特に当社では数多くご相談をいただいております。
精密機械加工のことでお困りの方は、OEM・EMSパートナーズ.comまでご相談ください。