インサート成形とは?複数部品を一体で成形するポイントを解説します!
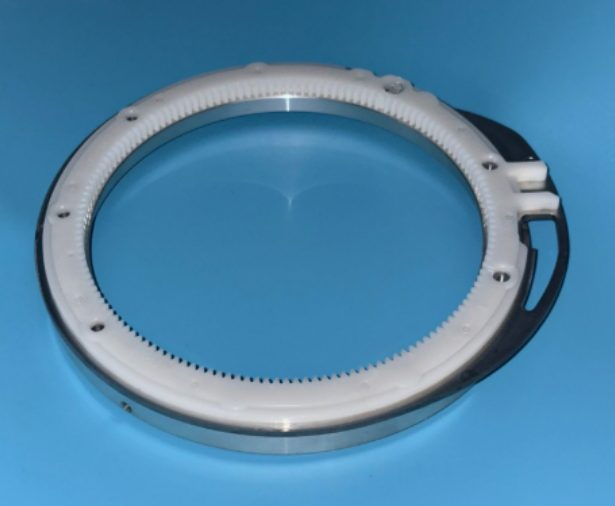
製造業の効率化や高品質化が求められる中、インサート成形が注目を集めています。これは金属などのインサート部品をあらかじめ金型内にセットし、プラスチックを射出して一体成形する技術です。従来は接着剤やネジによって組立てていた部品を一度の成形プロセスで仕上げられるため、製造コストの大幅削減や製品品質の安定化が可能となります。この記事では、インサート成形の仕組みから、メリット、OEM・EMSパートナーズならではのインサート成形のポイントまで詳しく解説します。
インサート成形とは?
インサート成形とは、金属やセラミックスなど、プラスチック以外の素材で作られたインサート部品を金型内にあらかじめセットし、その周りに溶融したプラスチックを射出成形機を用いて射出することで、インサート部品とプラスチックを一体成形する技術です。 インサート部品をプラスチックで包み込むことにより、両者を強固に結合させ、強度と柔軟性を兼ね備えた製品を製造できます。
インサート成形とアウトサート成形の違いとは?
インサート成形とアウトサート成形は、プラスチック成形における異なる成形方法で、金属部品や他の素材を組み込む際に使用されます。
インサート成形
- 方法:金型が開いているときに金属部品や他の素材を装着し、樹脂を注入して一体成形する方法です。
- 特徴:強度や耐久性が高く、接着強度の心配が少ないです。製品設計の自由度も高く、組立工程が不要になります。
- 使用機械:縦型の成形機が多く使用されます。
- メリット:組立工数の削減、製品の強度強化、精度の向上などがあります。
アウトサート成形
- 方法:先に成形したプラスチック部品に後工程で金属部品を組み込む方法です。
- 特徴:成形後に好きなタイミングで金属部品を取り付けることができ、熟練した技術が必要です。
- 使用機械:通常、成形後はプレス治具や半田ごてなどを使用します。
- メリット:金属部品を取り付けるタイミングが自由で、半田ごてを利用すると強固に固定できます。
インサート成形は一体成形による強度と精度が高く、組立工程が不要ですが、成形機に常時人が付く必要があるためコストが高くなることがあります。アウトサート成形は成形後の加工が柔軟で、熟練した技術が必要ですが、接着強度が低くなるリスクがあります。
インサート成形の成形プロセス
インサート成形は、以下のプロセスを経て行われます。
1.インサート部品の金型への配置
インサート部品を手作業またはロボットを用いて金型内に配置します。 正確な配置を保証するために、治具が使用されます。 自動化された配置は、大量生産に適しており、インサートの配置の一貫性、効率、精度を向上させます。 一方、手作業による配置は、少量生産に適しており、作業者が部品の品質やインサートの配置を目視で確認できるため、詳細な検査を行うことができます。 自動化システムにおいても、磁気センサーや画像認識システムを用いることで、インサートの配置や成形品の品質を自動で検査することができます。
2.溶融プラスチックの射出
溶融したプラスチックが射出成形機によって金型内に射出されます。 高圧で射出されたプラスチックは、金型の隅々まで充填され、金型内のベントから空気を排出することで、プラスチックがインサート部品に完全に密着します。
3.冷却と固化
プラスチックが均一に固化するように、金型は一定の温度に保たれます。 冷却段階で、プラスチックとインサート部品が融合し、一体化します。 この際、樹脂の収縮による亀裂や、樹脂がインサート部品内部に侵入することを防ぐために、適切な樹脂と成形条件を選択することが重要です。 特に、ガラス、コイル、電子部品など、変形や損傷しやすい製品の場合は、樹脂の選択が重要となります。
4.成形品のゲートからの分離
成形品は、ゲートと呼ばれる樹脂の流入経路から切り離されます。 ゲートの分離は、成形品に損傷を与えないように注意深く行う必要があります。
5.後処理
必要に応じて、バリ取り、塗装、印刷、追加工などの後処理が行われます。
インサート成形のメリット
インサート成形は、他の成形方法と比較して、以下のような利点があります。
組立時間の短縮
複数の部品をワンステップで組み立てることができ、生産サイクルと工程を大幅に削減できます。 従来の組立方法では、インサート部品をプラスチック部品に組み付けるために、複数の工程が必要でしたが、インサート成形では、これらの工程を1つにまとめることができます。
性能の向上
インサート部品とプラスチックの強固な結合により、製品の強度と耐久性が向上します。 これは、インサート部品とプラスチックが一体化することで、部品間のガタつきや緩みがなくなるためです。また、金属などの高強度材料を埋め込むことで、プラスチックの柔軟性とインサート部品の強度を組み合わせることができ、製品全体の機械的性能を向上させることができます。
コスト削減
組立工程の削減により、人件費や設備費を削減できます。 また、材料の使用量も削減できるため、材料費も削減できます。
小型化・軽量化
コネクタやファスナーが不要になるため、部品の小型化・軽量化が可能です。 例えば、自動車部品において、金属部品をインサート成形によってプラスチック部品に置き換えることで、軽量化による燃費向上に繋がります。
設計の柔軟性
金属部品とプラスチック部品を組み合わせることで、設計の自由度が高まります。 従来、金属材料でしか実現できなかったような複雑な形状の部品を、プラスチックで成形することが可能になります。
信頼性の向上
部品の緩みやずれのリスクを軽減し、製品の信頼性と耐久性を向上させます。 これは、インサート部品とプラスチックが一体化することで、部品間の相対的なズレがなくなるためです。また、溶融したプラスチックはインサート部品の周囲を隙間なく流れ込むため、プレス嵌合などの方法と比較して、金属インサートと溶融材料の間の隙間を狭く設計することができます。 これにより、複合製品の成形において、より高い信頼性を得ることができます。
多様な材料の使用
様々な種類のプラスチック樹脂を使用することができます。 熱可塑性樹脂、熱硬化性樹脂、エラストマーなど、用途や要求性能に応じて、最適な材料を選択することができます。
強固な接合
ンサート成形では、インサート部品を強固に固定することができます。 これは、ネジや接着剤を使用せずに部品を接合できるため、組立工程の簡略化、コスト削減、信頼性向上に貢献します。
インサート成形のデメリット
一方でインサート成形にはその性質から、以下のようなデメリットもございます。
設計の複雑さ
インサート部品の挿入角度や垂直度などを考慮する必要があるため、金型設計が複雑になります。 インサート部品を金型内に正しく配置するためには、金型の設計段階で、インサート部品の形状やサイズ、配置方法などを考慮する必要があります。
精度管理の必要性
インサート部品の位置決め精度が要求されるため、高度なプロセス制御が必要です。 インサート部品が正しく配置されないと、成形品の品質に影響を与える可能性があります。
樹脂の収縮による亀裂
インサート部品の周囲で樹脂が収縮し、亀裂が発生する可能性があります。 特に、ポリカーボネート樹脂を使用する場合に、この問題が発生しやすいです。
金型との適合性
金型とインサート部品が正しく適合していない場合、金型が破損する可能性があります。 インサート部品の形状やサイズが金型と合致していない場合、成形不良や金型の破損に繋がる可能性があります。
複数の製造技術の必要性
インサート成形は、プラスチック成形のみでなくインサート部品の製作が必要になるため、素材の調達やダイカスト鋳造、機械加工などが必要となってきます。
日東電気ならではのインサート成形体制
前述の通り、インサート成形を高精度で実現するには、金型設計の知識とプラスチック成形、インサート部品の設計製作が必要となります。OEM・EMSパートナーズ.comではダイカスト鋳造や精密機械加工によるインサート部品の製作から、インサート部品に対応した金型の設計製作・プラスチック成形まですべて自社内で一貫して対応できる体制を整えており、高精度で安定した品質を実現することが可能です。
この体制により、お客様には組立工数の大幅削減、品質の安定化、トータルコスト削減といったメリットを提供し、競争力の向上にも貢献しております。OEM・EMSパートナーズ.comは今後も一貫体制を強化し、より高付加価値なインサート成形品を提供してまいります。
日東電気が実施したインサート成形事例
回転部品(ダイカスト+射出成形)
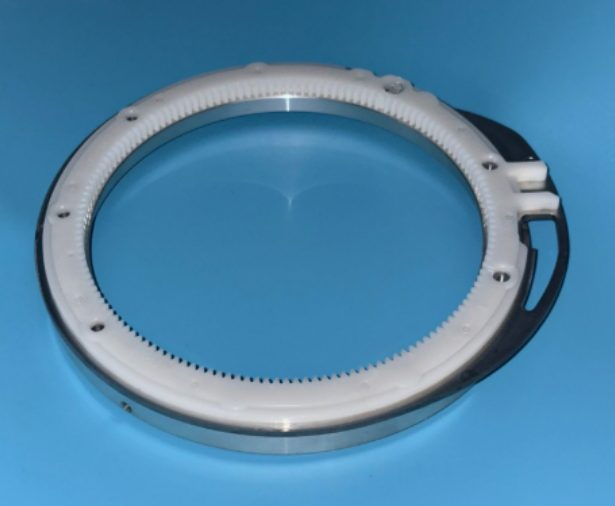
印刷機メーカー様より、印刷機内部で重要な役割を担うドラム回転部品の製造を受注いたしました。この部品は、従来、ダイカスト部品とプラスチック部品を別々に製造し、お客様側で組み立てていましたが、組み立て工数の削減と部品精度の向上が課題となっていました。
そこで、当社では、ダイカスト鋳造から機械加工、そしてプラスチック成形までの一貫生産体制を活かし、ダイカスト部品とのインサート成形による一体成形を提案いたしました。
日東電気ならではのプラスチック成形
金型設計~成形作業までの一貫対応
OEM・EMSパートナーズ.comを運営する当社は、プラスチック成形にも豊富な実績がございます。また、当社ではお客様からプラスチック成形のご依頼をいただいた際は、金型の設計・製作から行い、製品の量産までを一貫して対応しております。そのため、定期的なメンテナンスや製品形状が変更になった場合においても、同じ工場内での金型改造などの対応が可能となっているため、短納期且つ低コストで製品のご提供を可能にしております。
インサート成形・アウトサート成形にも対応
当社では様々な業界向けのプラスチック成形品に対応ができるよう、異種材料を組み合わせる必要がある場合や、高い強度や特殊な機能を要求される製品の製造に適しているインサート成形や、立型射出成形機を使い,金型内で金属プレートに金属などの部品を配置して一体成形するアウトサート成形も実施しております。
豊富な実績によるVA/VE提案
当社はプラスチック成形品について豊富な実績を有していることに加えて、常に最新のトレンドや情報を取り入れて製品を成形しております。そのため、お客様から製品データをいただいた際に起こりうる成形不良をリストアップし、事前に改善案を落とし込むことで、お客様にとって最適な成形の条件を対案いたします。
ワンストップ対応が実現する、高精度なエンプラ成形
OEM・EMSパートナーズ.comを運営する当社では、エンジニアリングプラスチックの成形にも対応しております。エンプラ成形は、ガスが発生しやすく、また金型やスクリューの摩耗が激しくなり、汎用プラスチックと比較して成形が困難とされています。
しかし当社では、材料特性を考慮した金型設計を行い、さらに射出成形機についても耐摩耗性スクリューを全成形機に搭載しており、ガラス繊維などの強化剤が含まれたエンプラでも問題なく量産成形が可能です
金型設計から製作、成形までワンストップ対応している当社だからこそ実現可能なのが、高精度エンプラ成形です。
インサート成形のことなら、OEM・EMSパートナーズ.comまで!
当サイトを運営する日東電気グループでは、金型設計製作からプラスチック成形・精密機械加工までをワンストップで対応しております。お客様のパートナー企業として様々な角度から技術提案をいたします。さらに当社では、部品の調達からアセンブリの工程管理まで、すべて請け負いますので、お客様の調達・管理コストの低減にも努めます。
インサート成形・プラスチック成形ことでお困りの方は、OEM・EMSパートナーズ.comまでご相談ください。