転造加工とは?切削加工との違いと転造ネジの特徴を徹底解説!
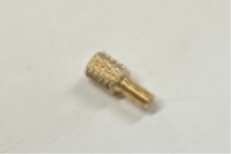
転造加工は、素材に圧力を加えて変形させ、ねじなどの形状を成形する塑性加工法です。切削加工とは異なり、素材を削らずに形成するため、強度・精度・生産性の面で優れたメリットがあります。
本記事では、転造加工の基本から切削加工との違い、転造ネジの特性まで、設計・調達担当者が押さえるべき技術情報を徹底解説します。
また、日東電気ならではの転造加工の対応力と技術提案力、実際の加工事例もご紹介しております。
転造加工とは?
転造加工とは、素材に圧力をかけて塑性変形させ、ねじなどの形状を形成する塑性加工法の一種です。切削加工のように素材を削るのではなく、素材を押し潰すことで形状を生み出すため、材料の繊維構造(ファイバーフロー)を維持しながら成形することができます。
転造加工は、主にねじ山の形成などに用いられており、特に強度・精度・量産性を重視する部品に最適です。転造加工は、回転する「ダイス」と呼ばれる工具で素材を挟み込むことにより、対象物に対して圧力をかけて形状を形成していきます。
転造加工の代表的な特徴
転造加工の特徴は、主に下記の通りです。
- ファイバーフロー(繊維流れ)を切断しないことで、強度が高い製品が得られる
- 工程時間が短く、量産に適している
これらの特長から、転造加工は自動車、家電、機械装置、建材など、幅広い分野で使用されており、近年では「切削加工から転造加工への工法転換」によるコスト削減や品質向上の提案も増加傾向にあります。
転造加工と切削加工の違いとは?
転造加工と切削加工は、いずれもねじや外形形状を形成するための加工法ですが、加工原理・強度・コスト・適用範囲において明確な違いがあります。
加工原理の違い
切削加工は、刃物などの工具で素材を削り取って形状を作る加工法です。微細な寸法調整や複雑形状の形成に向いており、1点モノや少量生産にも柔軟に対応できます。
転造加工は、素材に圧力を加えて変形させることで形状を形成する塑性加工です。切削と異なり、材料を削らないため、切りくずが出ず、素材のロスが抑えられます。
材料特性・強度の違い
転造加工は、素材内部のファイバーフローを保持したまま形状を形成するため、引張強度・耐摩耗性に優れるという利点があります。一方で切削加工では、仕上がり寸法は正確でも、加工硬化による強度は転造加工には劣るため、応力集中による破損リスクが高まることがあります。
加工時間・コストの違い
切削加工は、やや加工に時間がかかり、工具摩耗や切りくずの処理など付随コストが発生します。ネジ山加工のような場合は、工作機械の種類によっては量産性が劣る場合もあります。
転造加工では、加工時間が短く、1ストロークで加工完了するため、圧倒的な量産性があります。加えて、切りくずが出ないため、後工程の処理コストも不要です。
また、転造加工は工具(ダイス)を標準保有している業者であれば、イニシャルコストが不要または最小限で済み、コストパフォーマンスに優れます。
転造ネジの特長とメリットとは?
転造加工によって製造されたねじ(転造ネジ)は、切削加工によるねじと比較して、強度・量産性・品質安定性の面で優れた特徴を持ちます。特に自動車、電子機器、産業用装置など、信頼性とコストパフォーマンスの両立が求められる分野で多用されています。
ファイバーフローを活かした高強度
転造加工は、素材の金属組織(ファイバーフロー・メタルフロー)を切断せずに形状を成形します。このため、切削ネジと比較して、引張強度・ねじれ強度・疲労強度が向上します。
量産性と品質の安定
転造加工は、ダイスによる塑性成形でねじ山を形成するため、加工時間が非常に短く、サイクルタイムも安定しています。さらに、切りくずが発生しないため、後処理が不要で生産効率が高いのも特長です。
また、ダイスによる加工は寸法バラつきが少なく、表面粗さも均一化されるため、量産品における品質のばらつき抑制にも効果を発揮します。
転造ネジと切削ネジの違い
以上の内容をもとに、転造ネジと切削ネジの比較表をまとめました。
項目 | 転造ネジ | 切削ネジ |
---|---|---|
加工方法 | ダイスによる塑性変形 | 刃物による切削 |
強度 | ファイバーフロー維持で高強度 | 加工硬化あり |
表面粗さ | ダイス加工のため均一 | 工具摩耗があると荒れやすい |
コスト | 低コスト(材料ロス少) | 比較的高コスト(材料ロスあり) |
量産性 | 短サイクルで高い量産性 | 機械によっては1本ずつ加工 |
適用場面 | 大量生産・高強度用途 | 試作・少量生産・特殊形状対応時 |
このように、設計・調達の場面において、ねじの用途や性能要件に応じて、最適な工法を選定することが非常に重要です。当社では、切削と転造の両方の加工を行っており、それぞれのメリットを踏まえた技術提案が可能です。
日東電気ならではの転造加工における特徴
当サイトを運営する日東電気では、転造加工における技術対応範囲の広さ・コスト最適化・柔軟な生産体制を強みとし、多品種少量から量産品まで幅広く対応しています。また、設計段階からのVA/VE提案や、切削との比較による工法選定支援も行っており、調達・設計担当者様から高い評価をいただいています。
以下に、当社の転造加工における4つの主要な特長をご紹介いたします。
ダイス保有によるイニシャルコストの抑制
転造加工は通常、専用ダイスが必要であり、初期投資(イニシャルコスト)が課題となります。しかし当社では、各種ねじピッチ・形状に対応したダイスを多数保有しており、保有ダイスで対応可能な場合は専用ダイスのイニシャルコストを抑えることができます。これにより、試作段階でもコストを気にせず導入いただけます。
30種類以上の転造加工品への多品種生産対応
当社では、多数の転造機を保有しており、現在は30種類程度の転造加工品の量産に対応しております。1つの機械を占有することなく、多品種の転造加工に対応しておりますので、新規でお引き合いをいただいた転造加工品についても、当社では柔軟に製造対応することが可能です。
切削ネジと転造ネジの工法提案
当社では、転造加工のみならず、切削加工も自社内で対応しているため、ご要望に合わせた工法提案が可能です。機能とコストの最適バランスを実現するためには、場合によっては切削加工の方がコストパフォーマンスが良いという場合も多くあるため、当社では様々な要素を考慮した上で、最適な工法提案をさせていただきます。
精密機械部品の調達力・在庫力・対応力
転造加工や精密機械加工以外にも、当社ではメーカー様の調達代行という側面も持っており、お客様に代わって各種部品の自社調達も行っております。
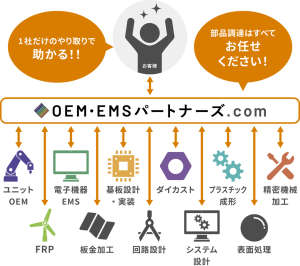
>>日東電気グループは、OEM・EMSのベストパートナーです。
精密機械加工に関する製品事例
続いて、実際に当社が製作した精密機械加工に関する製品事例をご紹介いたします。
スプール
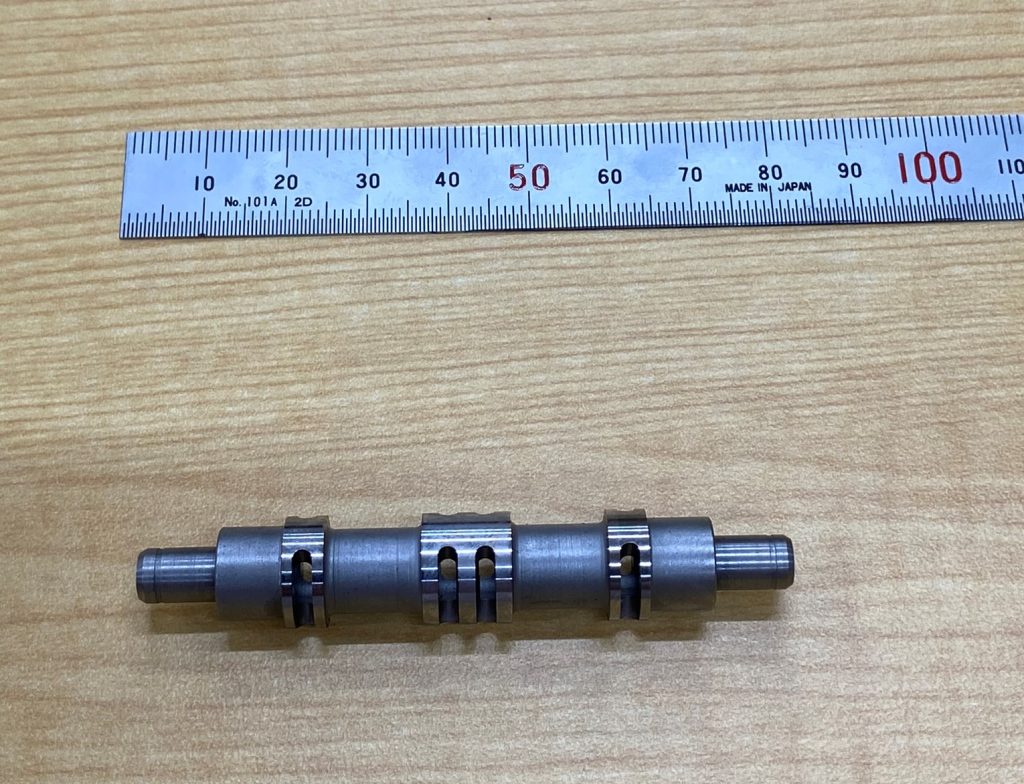
従来から取引のあるお客様から、油圧バルブ用部品の加工のご相談をいただきました。
該当する加工は長さがMAX110mm~MIN70mm、径φ10mm~φ18mmまでと範囲が広く、また形状に関しても40~50種の類似形状があったため、加工条件の選定に課題が多くございました。
当社では旋盤加工の為に専用バイトを製作して加工を実施。 また、検査工程においては始めに形状の確認・交差部の測定をすることで、同類形状の区分けをいたしました。
その後、各類似形状で共通使用ができる専用治具を設計・製作をすることで、類似形状ごとで加工条件を共通化し、オペレーションの最適化をすることでお客様に大変ご満足いただきました。
駆動軸
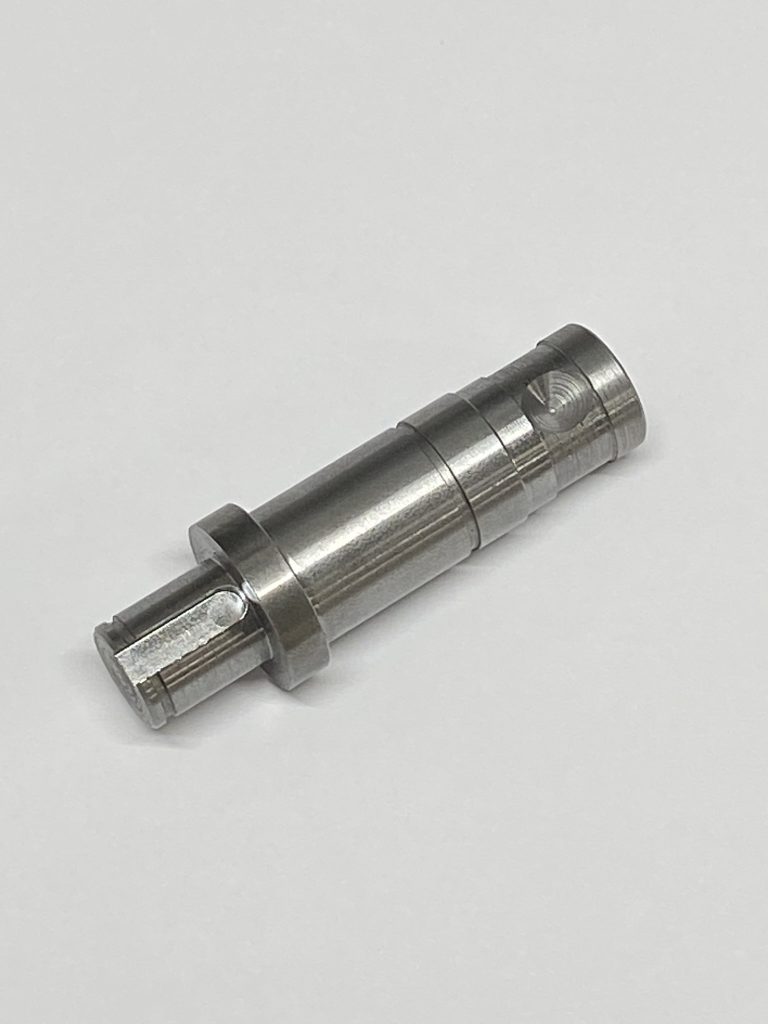
従来から取引のあるお客様から農機具部品の精密機械加工に関するご相談をいただきました。
ご相談をいただいた部品は加工精度が高く、コスト面でもお客様のご予算に納めるのが非常に厳しい状況でした。
そのため、通常ではNC旋盤加工・マシニング加工と複数工程で行う工程を、複合旋盤での対応を提案を行いました。
また、径方向にはめ合い公差h7が設定されていましたので、量産加工ではリングゲージを用い全数検査を行い、高精度の維持を実現しました。
また、キー溝部につきましてもブロックゲージによる全数検査にて対応しています。 本事例ではお客様のご要望であった高精度・低コストの双方を実現したことで、大変ご満足いただきました。
チェーンテンショナー
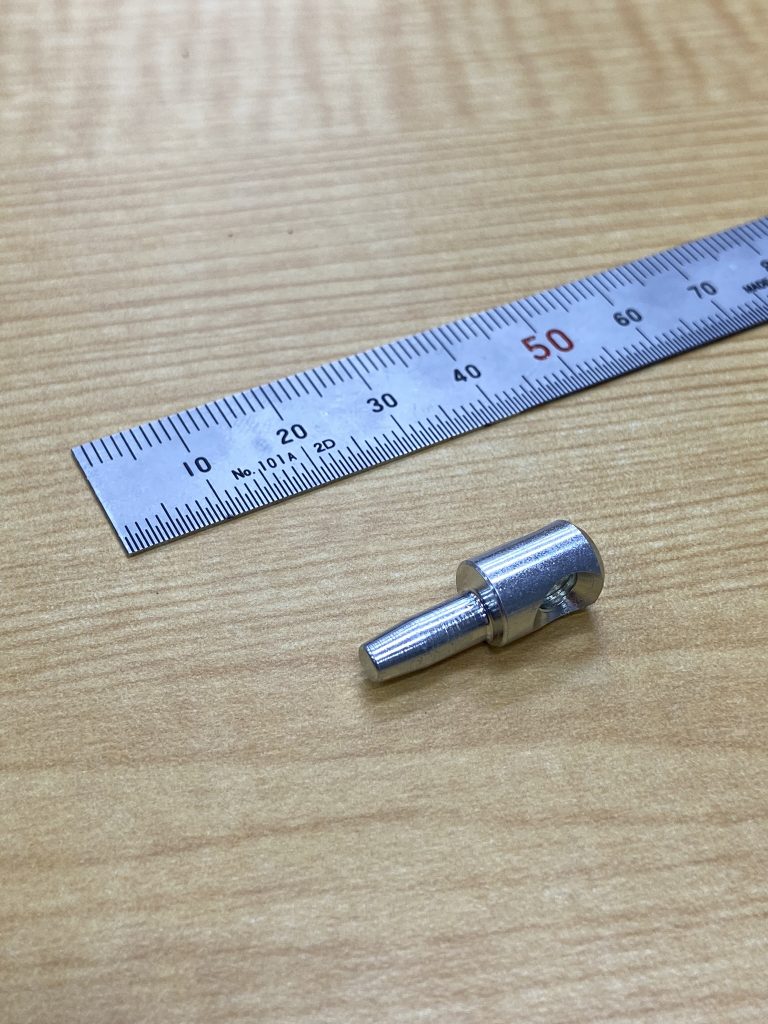
従来から取引のあるお客様から、チェーンソーのテンショナー部品の加工のご相談をいただきました。
該当部品は偏心形状であったため、偏心チャックを使用する非常に難度の高い加工でした。 また、側面にタップ加工が必要なために、旋盤加工後の自動タップ盤には専用治具を設計・製作して対応いたしました。
精密機械加工のことなら、OEM・EMSパートナーズ.comまで!
当サイトを運営する日東電気グループでは、精密機械部品の切削加工から最終の研磨工程までを一貫して行い、高精度な精密切削部品を数多く生産しています。当社では、アルミや銅の粘り気のある材質から、焼入れ材料の硬度の高いものまで豊富な加工実績がございます。また、航空機に使用されるタービンブレードのような大型の部品から、200mm以内の小型の部品までの加工可能サイズの範囲も広く、量産加工での精度は±100分の3mmと高精度での加工が可能です。
また機械加工については、単品小ロットの多品種少量生産における短納期を強みとしており、年間に数百種類の製品を製作しております。多くの部品加工業が取り回しを困難とするような製品について、特に当社では数多くご相談をいただいております。
精密機械加工のことでお困りの方は、OEM・EMSパートナーズ.comまでご相談ください。
関連した基礎知識
-
OEM・EMS・ODMの違いとは?
製造業界では「OEM」「EMS」「ODM」といった用語が頻繁に使用されますが、実際にはその定義や業務範囲、契約上の立場などが曖昧なまま使われていることも少なくありません。特に、これらのモデルを検討する...- ユニットOEM
- 電子機器EMS
2024年8月2日
-
センタレス研削加工とは?原理からメリット・デメリットまで解説!
センタレス研削加工とは? センタレス研削加工とは、円筒状のワークの外側を滑らかに加工する技術で、ワークの真ん中に穴を開ける必要がない研削加工の方法です。センタレス研削加工では、円筒形状のワークを、高速...- 精密機械加工
2024年6月17日