多層基板とビルドアップ基板の違いとは?
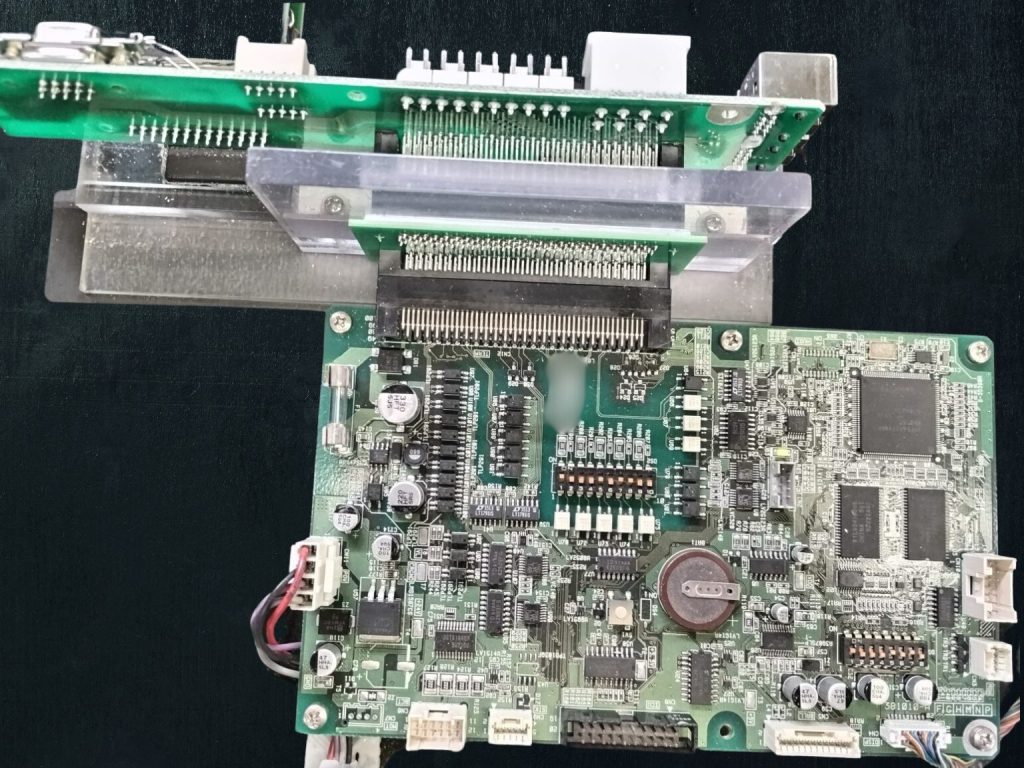
プリント基板の複雑さに直結してくるのが、プリント基板の構造です。構造別にプリント基板を分類すると、片面基板、多層基板、ビルドアップのように分類されます。
なかでも多層基板は、現在最も採用されている基板と言えます。多層基板は、複数の絶縁層と導体層で構成される電子基板のタイプです。一般的に、2つ以上の絶縁層とその間に配置された導体層からなり、導体層と絶縁層がミルフィーユ上に重なって構成されています。
そんな多層基板は、①多層貫通基板、②IVH基板、③ビルドアップ基板、という3種類に大きく分類することができます。
ここでは、プリント基板やその分類、なかでも多層基板の分類について、わかりやすく説明いたします。
プリント基板とは?
プリント基板は、電子回路を実現するための基板であり、絶縁性の高い基板材料(通常はガラスエポキシ樹脂やフリスクラムなど)に導電性のパターン(一般的には銅箔)が形成された基板です。プリント基板は、電子機器の信号伝達や電力供給を実現し、コンピュータ、携帯電話、家電製品など様々な産業で使用されます。
実際に当社でも、自動車車載基板・電力メーカー基板・医療機器基板・通信機器基板・自然エネルギー向け基板・蓄電装置基板・紙幣識別基板等、産業機器が使われる業界全般でプリント基板実装の実績があります。
プリント基板の種類一覧
プリント基板には様々な種類がありますが、
- 工程
- 材料
- 材質
- 構造
という4つの切り口で分類することができます。
プリント基板の種類:構造別
プリント基板の複雑さに直結してくるのが、プリント基板の構造です。構造別にプリント基板を分類すると、片面基板、両面基板、多層基板のように分類されます。
片面基板
片面基板は、現在は使用されることが少なくなっていますが、シンプルで基本的な回路基板です。回路は片面のみにあり、その構造もシンプルなため、コストは非常に安く抑えることができます。
両面基板
二層基板とも呼ばれる両面基板は、基板の裏側にもパターンが施された基板です。片面基板ではパターンが交差するのが困難になりますが、両面基板ではビアホールによって両面のパターンを電気的に接続することができます。そのため、片面基板よりも複雑なパターンの配線が可能になります。
しかし現在は、スピードや情報量も多くなっているため、基板を複数枚重ねた多層基板が多くなっています。
多層基板
多層基板は、複数の絶縁層と導体層で構成される電子基板のタイプです。一般的に、2つ以上の絶縁層とその間に配置された導体層からなり、導体層と絶縁層がミルフィーユ上に重なって構成されています。
多層基板は、高密度の回路や複雑な電子機器に使用されます。絶縁層は一般的にガラスエポキシ樹脂(FR-4)やポリイミドなどの材料で作られ、導体層は銅箔で構成されます。各層は、導通孔(ビア)を介して相互に接続され、信号や電力の伝達が可能となります。
多層基板の利点は、小型化、高い信号伝達速度、信号クロストークの軽減、電磁干渉の低減などがあります。また、複数の層を使用することで、配線の複雑さを減らし、回路の密度を向上させつつ、基板の表面積を最大限に活用できます。
多層基板の種類とは?
また、多層基板はさらに、
①貫通多層基板
②IVH基板
③ビルドアップ基板
という3種類に大きく分類することができます。
貫通多層基板
貫通多層基板は、多数の層を持ち、スルーホールを介して層間を接続する、もっとも一般的なプリント基板です。スルーホールとは、基板の上層から下層まで貫通した、銅めっきが施された300μm以上の穴のことであり、NCドリル等で基板に開けられて、導通用に使用されます。貫通多層基板は電子機器の小型化に貢献し、20層以上の構成が可能で、耐久性があるため、幅広い用途に使用されています。そのため貫通多層基板は、基板の小型化や電源、GNDの強化、配線密度の増加、インピーダンスコントロールが必要な場合に使用されます。また貫通多層基板は、銅箔の厚さや、板厚、層数など、様々な使用に対応することができます。
IVH基板
IVH(Interstitial Via Hole)多層基板は、貫通穴を使用せずに、必要な層間のみを接続する多層基板です。IVH基板では、スルーホールのような貫通穴ではなく、非貫通穴であるビア(Via)を使用します。
ビアには、ブラインドビアホールとベリードビアホールの2種類があります。ブラインドビアホールは、基板の表層と内層をつなぐビアで、基板表面では片側の穴が見えるビアです。4層IVH基板の場合では、L1-L2や、L3-L4のような層間接続をする際に使用されます。一方でベリードビアホール(インナービア)は、内層に埋め込まれて表層からは見えないビアです。4層IVH基板の場合では、L2-L3のような層間接続をする際に使用されます。
IVH基板では、ビアへの銅めっきが多くなり、銅箔厚が厚くなり、ファインパターンには対応できないという欠点があります。しかしIVH基板は、アートワークや配線密度の自由動画高く、高密度で高多層化されるため、配線やパッドを配置できる箇所が増え、小型化に効果的です。そのため、産業機器や車載機器等において、IVH基板の需要が高まっています。
ビルドアップ基板
ビルドアップ基板は、積み重ねていくという意味のビルドアップから由来する、多層基板の種類の1つです。多層基板は通常、機械加工で開けられた貫通穴であるスルーホールによって基板の層を接続していますが、ビルドアップ基板ではレーザービアによって接続されています。スルーホール接続の多層基板では、どうしても貫通穴の大きさはドリルなどの工具による制限がかかり、最小径はおよそ300μmほどとなりますが、レーザービア接続のビルドアップ基板では約100μmほどの小さな穴となり、より基板を小さくすることができます。また、このレーザーで開けられたビアはLVH(Laser Via Hole)と言います。
ビルドアップ基板では、コア層となるIVH基板に絶縁層を作り、その表面にプリプレグと導体を重ねて、必要な個所にLVHを作り、各層を導通させていきます。
ビルドアップ基板は、基板を小型化し、高密度な配線と多機能性を実現することが可能です。主にスマートフォンやパソコン、スピーカー、カーナビ、ゲーム端末など、小さく多機能な電子機器部品に多く使用されています。
貫通多層基板とビルドアップ基板の違いとは?
上記のように、貫通多層基板のビルドアップ基板の違いは、①層間接続の違い、②製作方法の違い、がございます。
層間接続については、貫通多層基板ではスルーホールで実施している一方で、ビルドアップ基板ではIVH[やLVHで実施しています。そして製作方法は、貫通多層基板のスルーホールはドリルによる300μm程度の貫通穴加工ですが、ビルドアップ基板ではレーザーによる100μm程度の小径の非貫通穴です。
日東電気ならではのプリント基板 設計・実装
当サイトを運営する日東電気では、これまでに数多くのプリント基板の設計・実装を行ってまいりました。日東電気だからこそ可能なプリント基板の設計・実装としては、下記のような特徴があげられます。
プリント基板の設計・実装に関する圧倒的な実績
これまでに日東電気では、様々な業界のお客様に向けて、多種多様なプリント基板の設計・実装を行ってきました。プリント基板の種類としては、ガラスコンポジット基板のCEM-3、ガラスエポキシ基板のFR-4が実績の大半を占めますが、高機能特性を持つテフロン基板・セラミック基板も実績としてございます。また最近では余り出回りませんが、紙フェノール基板の実装も対応しております。
鉛フリーはんだ・共晶はんだ、どちらのはんだ付け工程にも対応
鉛フリーはんだと共晶はんだは、各々が異なる特徴を持ち、異なる用途に向いています。環境への影響を最小限に抑えたい場合や高温環境下での使用が求められる場合には、鉛フリーはんだが適しています。一方、使いやすさやはんだ付けの信頼性が重視される場合には、共晶はんだが優れた選択肢となります。
ただし鉛フリーはんだは、共晶はんだの2,3倍のコストがかかるとされており、また融点も高いため、製造コストは時間的にも費用的にもかかってしまいます。
当サイトを運営する日東電気では、様々なはんだ付けに対応しており、お客様のご要望に応じて最適なはんだ工程や基板実装方法のご提案を行っております。はんだ付けには大きなプロセスとして、
- リフロー実装工程:表面実装(いわゆるSMT実装)
- フローハンダ工程:ソルダーリング装置やハンダ付けロボットを用いる
- マニュアルハンダ工程:人の手を介して行う
という3種類のはんだ工程がありますが、当社ではすべてのはんだ工程に問題なく対応しております。
鉛フリーはんだラインと共晶はんだラインにおける徹底したコンタミ防止
当社では鉛フリーはんだと共晶はんだ、どちらもラインを構築しておりますが、各ラインを別々に構築・管理しており、徹底したコンタミ防止対策を施しております。先述の通り、鉛フリーはんだは、RoHS規制によって開発が進められたはんだです。そのため、一定以上の鉛を含まないようにする必要があり、生産ラインにおいても対策が必要となります。共晶はんだと鉛フリーはんだを同じラインで実装すると、どうしてもコンタミが発生しかねません。
しかし当社では、共晶はんだは共晶はんだ専用のラインで基板実装を行っており、ライン単位で徹底したコンタミ防止対策を取っております。
現在は鉛フリーはんだを選択する電子機器も多くなっていますが、当社では現在でも共晶はんだのご依頼を多くいただいております。
混載実装への対応力
現在は電子機器も高機能化されており、その数量も増えていることから、生産性や低コストを重要視され、特に量産工程では表面実装が多く採用されています。一方で挿入実装は信頼性が高くストレス耐性も高い用途で必要とされます。
この両方を兼ね備えたのが、混載実装です。混載実装は、同一基板上でスルーホール(IMT、DIP)実装と表面(SMT)実装の両方を実施する実装方法です。表面実装と挿入実装では、実装できる部品が異なるため、多様な部品の実装が求められる場合に混載実装が使用されます。表面実装と挿入実装のどちらも必要な混載実装は、信頼性が高くストレス耐性も必要な製品を、なるべくコストを抑えつつ量産が必要な製品に採用されます。
そして当サイトを運営する日東電気は、混載実装の実績を数多く有しており、また混載実装の前工程であるアートワーク設計から、後工程の筐体設計・製造まで、ワンストップで対応しております。
リスクを徹底的に排除するVE提案
お客様が不安に思われる防水や火災などの機能面のリスクを徹底的に排除するためのVE提案や対策についても積極的にご提案を行い、エラーが生じない、万が一生じてもすぐにエラー発見できるEMS生産体制を構築いたします。UL規格、IEC規格、EMC規格、PSEマーク、S-JET認証、RoHS指令、系統連系保護装置等認証、第三者認証制度、JQA(日本品質機構)など、各種規格や制度に則って、安心いただける電子機器EMSメーカーとして基板設計・実装を行っております。
工程FMEAにも対応
当社ではお客様のご要望に合わせて、工程FMEAにも対応しております。FMEA(Failure Mode and Effects Analysis)は、製品やプロセスにおける各種の障害や故障の可能性を予測し、その結果に対する影響を定量的に評価する手法です。FMEAは、日本語では故障モード影響解析と呼ばれます。製品の設計段階からプロセスの改善後まで、あらゆる段階での障害や故障のリスク評価を行い、予防的な対応策を立てることで、製品やプロセスの品質を向上させることができます。
基板関連部品の調達力・在庫力
基板実装には様々な電子部品が必要となりますが、当社では電子機器メーカー様の調達代行という側面も持っており、お客様に代わって基板周辺部品の自社調達も行っております。
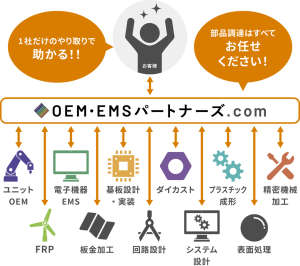
コイルや抵抗、ハーネスなどの電子部品から、プラスチック筐体、板金筐体などの組立工程に必要な部品まで、すべて調達いたします。
>>日東電気グループは、OEM・EMSのベストパートナーです。
基板設計・実装に関する技術提案事例
続いて、実際に当社でご提案した、基板設計・実装技術提案事例です。
ロボットはんだ付けによる基板実装で生産性向上&品質向上
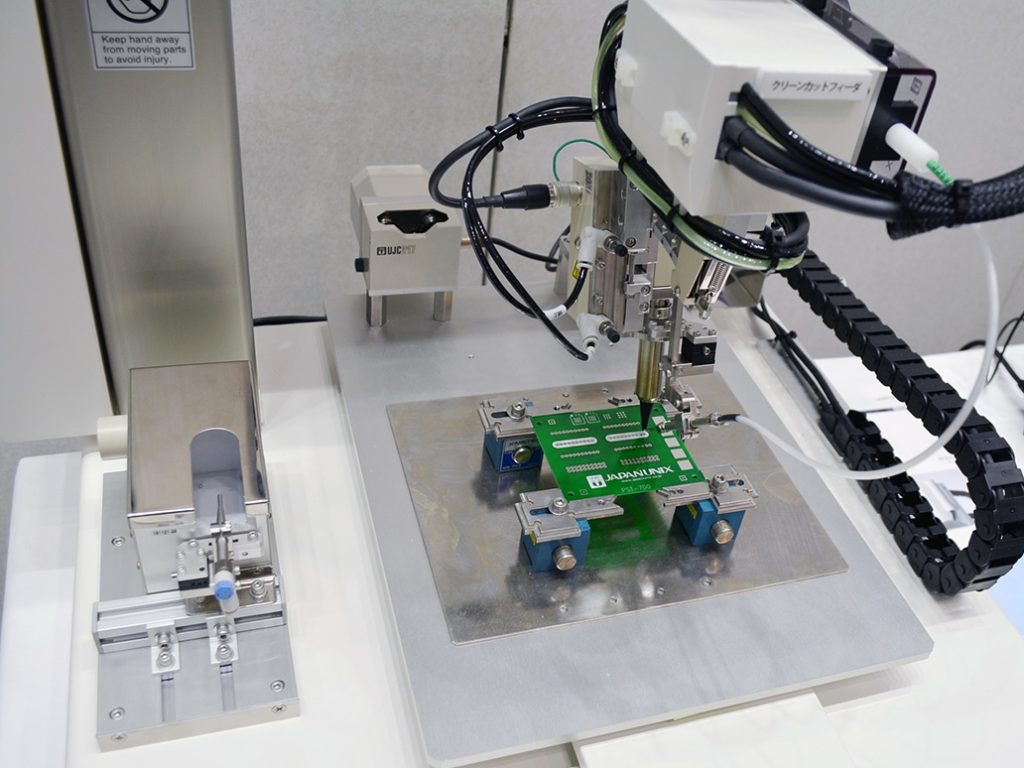
大手自動車メーカーのお客様から、ピン数の多いコネクタはんだ付けを伴う基板実装のご相談をいただきました。ピン数が多くなればなるほど工数はかかりますが、手作業で実施するとどうしても品質のバラツキやヒューマンエラーが生じてしまいます。
そこで当社では、ロボットはんだ付けによる基板実装のご提案をいたしました。当社ではJAPANUNIX製のはんだ付けロボットを2台保有しており、数量やはんだ付けの内容に基づいてご提案をしております。
人的作業からロボットによるはんだ付け作業に変更することで…
基板設計・実装に関する製品事例
続いて、実際に当社が製作した基板設計・実装に関する製品事例をご紹介いたします。
モバイルカー向け基板&ダイカスト筐体組立実装
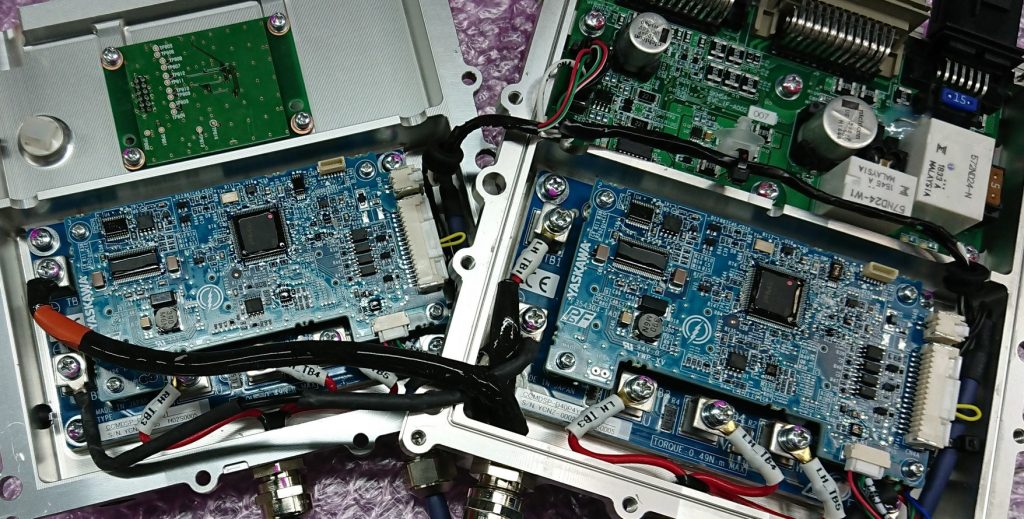
こちらは次世代モバイルカー向けの基板&ダイカスト筐体組立実装事例です。基板サイズは200×200、製品サイズは500×500×200で、100個/月の量産品でした。
次世代モバイルカー開発の担当者から直接お問い合わせをいただき、回路図はお客様にて作成・支給いただきました。当社の小山工場でアートワーク設計から基板実装、ハーネス加工まで対応し、水戸工場でダイカストケース製造(金型はお客様より支給)を実施いたしました。その後、組立から電気検査までワンストップで対応いたしました。
シニアカー用インバーターユニット
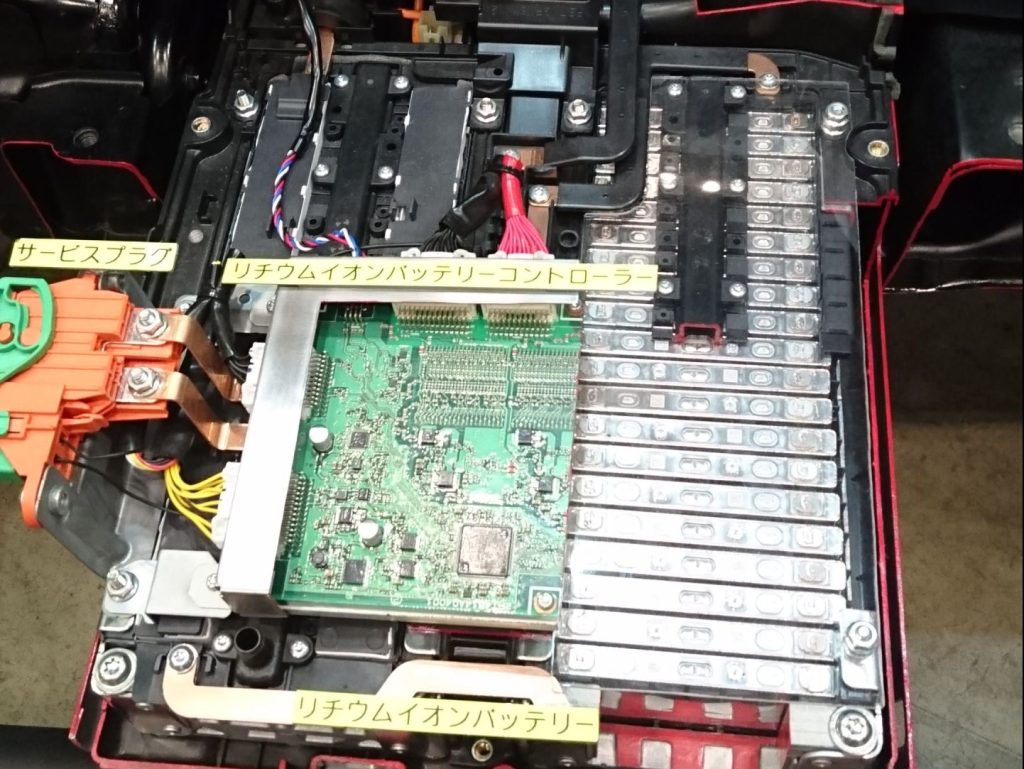
こちらはシニアカー用インバーターユニットです。基板サイズは180×150、製品サイズは230×200で、100個/月の量産品でした。
シニアカーの開発担当者の方からご相談をいただき、当社の小山工場でアートワーク設計から基板実装、ハーネス加工まで対応し、水戸工場でダイカストケース製造(金型はお客様より支給)を実施いたしました。その後、組立から電気試験までワンストップで対応いたしました。
基板設計・実装のことなら、OEM・EMSパートナーズ.comまで!
当サイトを運営する日東電気グループでは、基板アートワークの設計から混載実装、各種検査までをワンストップで対応しております。国内大手メーカー様の基板設計・実装工場として、当社をOEM・EMS先に選定いただきましたら、お客様のパートナー企業として様々な角度から技術提案をいたします。さらに当社では、部品の調達からアセンブリの工程管理まで、すべて請け負いますので、お客様の調達・管理コストの低減にも努めます。
基板設計・実装のことでお困りの方は、OEM・EMSパートナーズ.comまでご相談ください。
関連した基礎知識
-
多層基板とビルドアップ基板の違いとは?
そんな多層基板は、①多層貫通基板、②IVH基板、③ビルドアップ基板、という3種類に大きく分類することができます。 ここでは、プリント基板やその分類、なかでも多層基板の分類について、わかりやすく説明いた...- 基盤設計・実装
2024年4月19日
-
電子機器の設計・製作に必要な安全規格まとめ
電子機器の設計・製作に必要な安全規格 一覧 電子機器の設計・製作をするには、様々な認証規格をクリアする必要があります。ここでは、電子機器EMSを行う当社が実際に関係する認証規格を一覧にラインナップしま...- 基盤設計・実装
2024年2月23日
-
プリント基板の種類一覧をご紹介!
プリント基板とは? プリント基板は、電子回路を実現するための基板であり、絶縁性の高い基板材料(通常はガラスエポキシ樹脂やフリスクラムなど)に導電性のパターン(一般的には銅箔)が形成された基板です。プリ...- 基盤設計・実装
2024年2月16日
-
プリント基板とは?種類から設計・製造工程まで解説!
プリント基板とは? プリント基板は、電子回路を実現するための基板であり、絶縁性の高い基板材料(通常はガラスエポキシ樹脂やフリスクラムなど)に導電性のパターン(一般的には銅箔)が形成された基板です。プリ...- 基盤設計・実装
2024年1月8日
-
基板アートワーク設計とは?
基板アートワーク設計は、基板製造で最も重要なステップの1つである、基板配線パターンのデザインプロセスです。しかし単純な回路以外では、基板設計のノウハウがない場合、基板を作ってしまった後に様々な不具合が...- 電子機器EMS
- 基盤設計・実装
2024年4月19日
-
共晶はんだと鉛フリーはんだを徹底比較!
はんだとは? はんだとは、金属を溶融して接合するための材料で、電子機器の製造において不可欠な存在です。主に基板に使用され、電子部品の固定および電気的接続を確保します。基板とは、電子機器内部にある薄い絶...- 基盤設計・実装
2024年1月8日
-
SMTとIMTの違いとは?
電子機器の進化と需要の増加に伴い、基板実装に関するニーズも増加しています。その中でも、SMT(表面実装)とIMT(挿入実装)の違いや、どちらも行う混載実装が注目を浴びています。今回は、SMTとIMTの...- 電子機器EMS
- 基盤設計・実装
2023年9月21日