OEM・EMSパートナーズ.comの
「基板設計・実装」
アートワーク設計からハーネス加工、SMT・IMTの混載実装、鉛フリーはんだまで幅広くワンストップ対応!
OEM・EMSパートナーズ.comでは、基板設計から実装まで幅広くワンストップ対応しております。設計段階は、はんだ上がりを配慮したアートワーク設計から、メタルマスクの開口設定まで、実装・はんだ工程を考慮して仕様書に基づいて基板設計を行います。実装工程は、SMT・IMT工程の混載実装に対応しており、自社で治具の設計・製作も行います。はんだ付けは、自動はんだ槽ラインから、ロボットはんだ付け、さらに環境に配慮した鉛フリーはんだまで、お客様の基板の使用用途に合わせて最適な基板実装方法を選定いたします。
基板の使用環境に基づいた防水・防湿・防塵対策
当社で設計・実装を行う基板は、産業機器から医療機器、高電圧電源装置など、様々な場所で使用されています。これらの使用環境によって、求められる機能は異なります。
当社では基板の使用環境に合わせて、防水・防湿・防塵対策などを実施いたします。環境によってはゴムパッキンよりもシリコンコーキングの方が適していたり、逆に吸湿防止対策をするなど、様々な対策提案を当社からも実施いたします。
また基板ケースについても、板金筐体ケースが多くなりますが、ご要望に合わせてダイカストや樹脂など、ケース材質や形状についてもご提案させていただきます。
各種認証・規格への対応力
OEM・EMSパートナーズ.comでは、当社の基板が採用された製品が安心して市場で使用いただけるように、様々な認証規格を取得しております。直近で多いのは、UL規格へ対応するために鉛フリーはんだで実装したり、医療機器のために医療器製造業許可を取得、さらにはS-JET認証、系統連系保護装置等認証などの認証・規格への対応を進めております。
より厳しい業界になると、高電圧電源装置では電気機器安全法に適合する導通試験を実施して品質保証を行い、FMEA(故障モード影響解析)を実施して生産段階でエラーが発見できる体制を構築するなどの対策も行っています。
お客様の基板実装OEM工場として安心してお任せいただけるような体制づくりを行っていますので、基板実装でお困りの方はぜひご相談ください。
日東電気 小山工場による基板設計・実装の一貫対応力
当サイトを運営する日東電気では、小山工場にて基板の設計・実装を一貫対応しております。
コンタミ防止をする工場レイアウト
基板実装を行う日東電気の小山工場では、下記のような工場レイアウトを組んでおり、自動部品棚を活用した部品自社調達(Aブロック)から、各種検査(Bブロック)、共晶はんだ、鉛フリーはんだの自動はんだ槽によるライン実装(Cブロック)まで、すべて一貫対応しております。
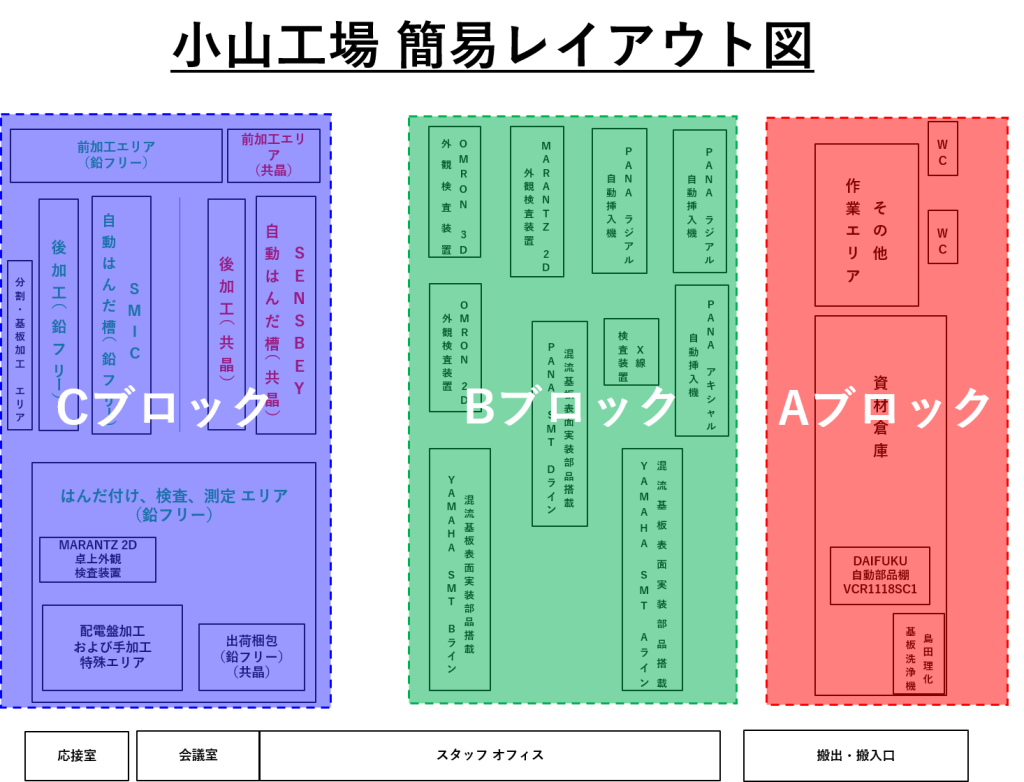
詳細は下記の通りです。自動部品棚を中心とした資材倉庫や、組立アセンブリのみの製品に対応するAブロックに、SMTラインをBブロックに、そしてコンタミ防止をしたはんだ工程&検査工程をCブロックに、それぞれ配置しております。
DAIFUKU製 自動部品棚
DAIFUKU製 自動部品棚「VCR 1118SC1」は、省スペースですが 1基で最大360アイテムのアイテムを格納できます。当社では4基あり、合計 1,440アイテムの収納が可能です。専用パソコンで収納品のストック場所を管理しているため、スムーズに必要な部品の取り出しが可能です。また一括払出も可能なため、通常の部品棚より作業時間の短縮ができます。
また調達部品について、主要の取引先商社は現在 80社以上ございます。主要メーカー1次代理店と、多数メーカーの取り扱いがある商社、どちらとも調達が可能で、一括見積・購入が可能な点が、日東電気の調達力を支えています。
SMTライン(スクリーン印刷・チップマウンター・リフロー)
当社ではSMTラインを2ライン保有しております。SMT搭載機と鉛フリー半田対応型(N2)リフローを含めて、 3つのラインを保有しております。0603チップから52ミリ角のBGAなどの大型異形部品まで、高精度の搭載が可能です。
YAMAHA マウンター 基本データ
・搭載(実装)能力
現在、1シフト(8~10h 稼働)体制のため、現ショット数×約 1.5倍の余力があります。
・機種切り替え
A・Bラインともに 一括台車を使用しているため、段取り時間を大幅に短縮しています。
・印刷品質
クリームはんだ印刷後に、3D 検査機をインラインで装備しているため、印刷品質を保証する事ができます。
・リフロー品質
2ラインともN2 仕様のため、お客様のご要望に合わせて 大気・N2 の生産が可能です。
アキシャル・ラジアル自動挿入機
アキシャル・ラジアル自動挿入機は、SMT などの自動機では挿入できないリード部品を自動挿入し、リードカット & クリンチできる装置です。当社では3台保有しております。
世の中の製品は省力化や軽量化などの機能に合わせて進化をしていますが、いまだに古い生産機種 (部品変更や設計変更できない機種)も存在します。時代とともに無くなっていく古い設備を大切に取り扱うことで、当社では他社には出来ないディスクリート部品の自動挿入生産を可能にしています。ディスクリート部品は、アキシャル ( 横型部品 )・ラジアル ( 縦型部品 ) ともに対応が可能です。
フローはんだ付け装置(共晶はんだ、鉛フリーはんだ、コンタミ防止)
フローはんだ付け装置は、棒はんだを槽内で溶かし、基板を通過させて挿し部部品のリードに対し、はんだ付けを行う装置です。当社では、SENSBEY 製のILF-350CZ(共晶はんだ専用)と、千住金属工業製の SPF-300(鉛フリーはんだ専用)を保有しております。
小山工場ではコンタミ防止のために、鉛フリーはんだ、共晶はんだ、それぞれのはんだを用いる専用エリアと生産設備を使用しています。更なる混入防止策として、社内の流動で使用する「現品票」を色分けし、最終工程までの「可視化」を行っています。
OMRON製 基板外観検査装置
OMRON製 基板外観検査装置「VT-S1080-V2」は、既存の2次元式の検査装置よりも優れており、部品の搭載やはんだ状態などを、3次元方式で検査できる3D3D 自動検査装置(AOI:“Automated Optical Inspection)です。
メーカ | OMRON |
項目 | 確認結果 |
装置名 | VT-S1080-V2 |
装置サイズ(W mm) | 1180 |
装置サイズ(D mm) | 1450(MAX前:+930)、(MAX後:+980) |
装置サイズ(H mm) | 1500 |
電源電圧 | 200 |
消費電力(KVA) | 2 |
カメラ《直視》(Mpix) | 25 |
カメラ《斜め》(Mpix) | 5 |
カメラ分解能《直視》(μm) | 12.5 |
カメラ分解能《斜め》(μm) | 10 |
撮影速度(mm2/sec) | |
高さ計測範囲(mm) | 25.4 |
高さ計測範囲(文字検査) | |
サイドカメラ | 有り |
Z軸機構 | 無し |
照明 | RGB方位点灯+白色点灯 |
対象基板(W mm) | 50~510 |
対象基板(D mm) | 50~680 |
対象基板(厚さ mm) | 0.4~4 |
対象基板(重さ Kg) | 4 |
アップグレード | ワンプラットフォームによりアップグレード可能 |
搬送クリアランス | 上50mm 下50mm |
繰り返し計測制度 | |
検査プログラム | PRG工数/スキル最小化 |
データコンバート | マウンタデータをコンバート、PWB読み取り、AI検査ロジック |
挿入部品検査 | 対応可 |
余剰部品検査 | 異物検査対応可 |
自己診断 | リモートメンテナンス *モデム含め、400K円装置自己診断: キャリブレーション治具の他、 装置内部に設備状態確認板を保持。 基準逸脱時にはアラートを出す。 |
周辺装置(デバッグ等) | v-TS:検査プログラム作成端末 |
周辺装置(NG判定) | v-CA:修正支援端末 |
修正(実画像)端末 | WIT IP4000と接続可能 |
検査データの活用 | Q-up、品質改善支援システム、車載業界要求対応 |
ソフトウェア(デバッグ) | 規格値をダイレクトに適用、定量検査~IPC規格準拠 |
ソフトウェア(ライブラリ)1 | 機種をまたいでの検査基準共通化 |
ソフトウェア(ライブラリ)2 | プログラム履歴管理、ロールバック機能 |
・業界随一の検査精度の高さ
MDMC照明+MPS位相シフトを組み合わせたオムロン独自のはんだ形状復元技術により、高精度はんだ検査が可能です。はんだ検査の精度の高さから、車載業界をはじめとする高品質業界で多数の導入実績がある装置です。
・人のノウハウに依存しないスキルレス運用
検査PG手順はシステム化されており、誰が作成しても手戻りや設定もれがない仕組みが構成されています。加えて、不良画像蓄積や検査基準共通化により、人のミスによる見逃し・見過ぎが防止できる。総じて、人のスキルに依存しない運用が可能です。
・装置を止めない生産性の高い運用
事前の基板撮像時にすべての照明条件で画像を取得するため、完全オフラインでのティーチングが可能で、条件変更のたびに本体設備を止める必要がありません。
「基板設計・実装」
のパートナーサービス
ケーススタディでわかる!
「基板設計・実装」
に関する技術提案
-
- 基盤設計・実装
ウィスカ対策として、鉛フリーはんだから共晶はんだへ変更して品質向上
ウィスカの発生が問題となっていた車載用基板実装において、はんだを鉛フリーはんだから共晶はんだに変更することで、ウィスカの発生を抑制することに成功した技術提案事例です。
-
- 電子機器EMS
- 基盤設計・実装
- プラスチック成形
電子機器の強度向上&防水・防塵対策
防水・防塵対策と強度向上が必要だった車載用電子機器に対して、基板工場と成形工場が連携して、さらにシリコーン塗布自動設備を開発することで、強度向上&防水・防塵対策を同時に実現した技術提案事例です。
-
- 電子機器EMS
- 基盤設計・実装
- FRP
板金 ⇒ FRPに材質変更して塩害対策&コストダウン&軽量化
塩害対策と軽量化が必要だった船舶機器に対して、ケースを板金 ⇒ FRPに材質変更することで錆対策を不要にしてコストダウンを実現し、さらに軽量化や強度向上にもつなげることができた技術提案事例です。
-
- 電子機器EMS
- 基盤設計・実装
基板&ケースの両面から防水・防湿対策
防水・防湿対策が必要だった急速充電装置に対して、基板とケースの両面から防水・防湿対策を行った技術提案事例です。
OEM・EMSの基礎知識
-
ウィスカとは?ウィスカの対策として共晶はんだが有効な理由とは?
ウィスカとは? ウィスカ(Whisker)とは、錫(Sn)や亜鉛(Zn)などの金属メッキ表面から自然発生的に成長する微細な針状の金属結晶のことを指します。文字通り「ヒゲ」のような細長い形状を持ち、電子...- 基盤設計・実装
2025年3月11日
-
フローはんだ付けとは?リフローとの違いから不具合&対策まで解説!
そもそも”はんだ付け”とは? はんだとは、金属を溶融して接合するための材料で、電子機器の製造において不可欠な存在です。主に基板に使用され、電子部品の固定および電気的接続を確保し...- 基盤設計・実装
2025年1月28日
-
パワーコンディショナー(Power Conditioner)とは?
パワーコンディショナー(Power Conditioner、「パワコン」または「PCS」とも呼ばれます)は、蓄電池や太陽光発電システムなど再生可能エネルギーにおいて、直流電力を交流電力に変換し、家庭や...- 基盤設計・実装
2024年9月17日
-
共晶はんだ実装で必要不可欠なコンタミ防止対策
共晶はんだとは? 共晶はんだ(読み方:きょうしょうはんだ)は、主に錫(Sn)と鉛(Pb)の合金から構成されています。一般的な共晶はんだの組成は、錫と鉛がおよそ6:4の比率で成分が混合されています。共晶...- 基盤設計・実装
2024年5月15日
「基板設計・実装」
に関するよくある質問
-
共晶はんだと鉛フリーはんだの違いはなんですか?
鉛フリーはんだと共晶はんだは、各々が異なる特徴を持ち、異なる用途に向いています。環境への影響を最小限に抑えたい場合や高温環境下での使用が求められる場合には、鉛フリーはんだが適しています。一方、使いやすさやはんだ付けの信頼性が重視される場合には、共晶はんだが優れた選択肢となります。
ただし鉛フリーはんだは、共晶はんだの2,3倍のコストがかかるとされており、また融点も高いため、製造コストは時間的にも費用的にもかかってしまいます。
共晶はんだ 鉛フリーはんだ 融点 約180℃ 約220℃ 成分 鉛を含む(鉛、錫、銀等) 鉛を含まない(錫、銀、銅、ニッケル等) ぬれ性 ぬれ広がりがよい ぬれ性はよいが、共晶はんだには劣る コスト 〇(低コスト) △(高コスト) 仕上がり 表面に金属光沢がある 金属光沢がなく白っぽい 比重 鉛があるため重い(7.4から11前後) 鉛がない分軽い(7.4から8.4前後) 機械的強度 (引張強さ) 10前後から43MPa前後 機械的強度は鉛がない分強い 電気抵抗 電気抵抗は成分により異なるが13前後から55前後(10-2μΩm) 電気抵抗は鉛はんだより小さい 実装品質 高品質 高品質は望めない 利用分野 航空・鉄道・発電など、高い信頼性が求められる公共・インフラ分野 電子部品、家電製品のほぼすべて -
共晶はんだとはどのようなはんだですか?
共晶はんだは、Sn(錫)63%とPb(鉛)37%の合金で構成されたはんだです。
ひと昔前(約20年前)までは、基板実装には鉛を含む「共晶はんだ」が一般的に使われていましたが、環境面へ悪影響を与えるとして、RoHS指令により電子部品の多くで使用が制限されたため、2000年以降に鉛を含まない「鉛フリーはんだ」が誕生し、現在は鉛フリーはんだが主流のはんだとして幅広く使用されています。
しかし性能面や信頼性の観点から、共晶はんだが必要な分野はいまも残っており、高度な信頼性が要求される場面では特に重宝されています。
-
共晶はんだと鉛フリーはんだの識別を、どのように管理していますか?
当サイトを運営する日東電気では、共晶はんだの基板実装を数多く行っておりますが、下記のような共晶はんだ実装のコンタミ防止対策を取っています。
・コンタミ防止をする工場レイアウト
・色でわかりやすく判別可能な現品票
詳細は下記をご覧ください。
-
CEM-3とFR-4の違いはなんですか?
当社でよく使われる基材は、主に下記の通りです。
・ガラス布基材エポキシ樹脂(FR-4)
・複合基材エポキシ樹脂(CEM-3)
FR-4の材質は、ガラスエポキシ材(ガラス繊維製の布)+エポキシ樹脂を含浸したもので、CEM3の材質は、ガラスコンポジット材+エポキシ樹脂を含浸しています。顕微鏡で見ると切り揃えられたガラス繊維を重ねたように見えます。
材質の特徴としては、FR-4は非常に硬く、耐久性が非常に高い反面、専用工具や機械がないと加工が難しいです。しかし汎用性が高く信頼性があるため、様々な用途で使用されています。
CEM-3は、FR-4よりも耐久性は劣りますが、加工性はベークとエポキシ材の中間くらいとなっております。
-
基板のアートワーク設計におけるポイントはなんですか?
一口に、基板設計と言っても、回路図を見てつなげていくだけでも、基板の形にはなってしまいます。しかし、単純な回路以外では、基板設計のノウハウがないと、基板を作ってしまった後、不具合が発覚してしまう場合が考えられます。これを未然に防ぐには、経験とスキルが最も重要です。
例えば、何十アンペアの電流が流れ何百ボルトの電圧がかかる回路の場合、パターン幅、パターン同士との間隔を考慮しないと、誤動作を起こしたり、電子部品が破壊されたりします。そのためにも、回路図・部品表・ネットリスト・製品設計コンセプトとなる仕様書が必要となります。
基板設計は電子機器の主要部品となる、電子回路を構成しているプリント基板を設計することを指します。電子回路に利用する電子部品を実装する場所を決め、それぞれの電子部品を配線するためのアートワークを作成します。基板を製作するには回路図を作り、それを元に基板設計をして、初めてプリント基板が製作されます。
-
SMTとIMTの混載実装を検討していますが、実装における注意点はありますか?
代表的な基板実装方法として、挿入実装(IMT)と表面実装(SMT)があります。挿入実装では、リード部品(DIP部品)をスルーホールに挿入し、部品を実装します。表面実装では、スルーホールを用いずに、基板表面のパッドにSMT部品の電極を接合します。
混載実装とは、同一基板上で上述の挿入実装(IMT)と表面実装(SMT)のどちらも用いて、基板実装を行う方法を指します。表面実装と挿入実装では、特徴や実装できる部品が異なります。そのため、多様な部品の実装が求められる場合などは、この混載実装が必須となります。
混載実装では、挿入実装、表面実装のどちらの工程も必要であるため、実装工程のステップは非常に多くなります。実装ステップとしては、通常、表面実装(SMT)が先に行なわれ、その後に挿入実装(IMT)が行なわれます。
SMT実装にて一度温度の掛けた基板は IMT実装にて再度温度が掛かるとハンダの再溶融や部品そのものが破壊される事もあるため 適切な温度管理が必要になります。その為にハンダ槽の温度プロファイル管理や条件に応じたDIPバレットの使用により 全体に熱を再度かけずハンダ付けを必要とするポイントのみ熱をかける手法など様々な工夫での実装技術と熱の管理がポイントとなります。
-
高温環境で使用したい基板には、どのようなはんだ付けが良いでしょうか?
高温環境で使用する基板の対策としては、はんだ付けよりも、むしろ基板設計・筐体設計が最も重要になります。
電子回路を搭載した筐体を製作する場合、基板から発生する熱によって電子部品が破損しないよう設計することが重要です。最近は、特に電子回路の微細化・筐体サイズのコンパクト化に伴い、電子回路の熱対策は重要性を増しています。
具体的な基板設計・筐体設計による高温環境への対策としては、
・部品配置の見直し
・電流を流すための銅箔パターン配置の見直し
・筐体形状や材質の見直し
・ヒートシンクや冷却ファンの追加など 基板のみならず筐体全体での放熱性の確保を考慮した設計が必要とされます。
-
裏面はんだにも対応可能ですか?
チップ部品実装の表面実装工程(SMT) では、表裏2面の実装は一般的に行われてます。ディスクリート部品を実装する (IMT)工程においても、裏面はんだについては、フローはんだ槽を用いて、DIPキャリア治具にて必要な箇所にはんだ付けを行っております。またロボットや人間がはんだ付けを行うマニュアル工程でも、裏面はんだは一般的な内容です。
-
フローはんだ槽のメリット・デメリットを教えてください。
フローはんだ付けのメリットは、なんと言ってもその生産効率の高さにあります。 基板を連続投入することで、 20~30秒のサイクルタイムで生産が可能になります。 フローはんだ付けは、リード部品からチップ・SOP部品まで 広くはんだ付け対象にできます。
フローはんだ槽のデメリットや不具合の最も大きな要因は、基板の搬送角度が大きいことによる熱不足やはんだの乱流です。 鉛はんだよりも流動性の劣る鉛フリーはんだで重要なのは、フラックスの塗布条件とフラックスを劣化させない範囲での十分な加熱条件です。これはブローホール・ピンホールのみではなく、赤目やブリッジなどの不具合対策にも通じる条件でもあります。 -
鉛フリーはんだと共晶はんだ、どちらの方がコストメリットがありますか?
共晶はんだは、鉛フリーはんだと比較して融点が低く、濡れ性が良いため、高品質に仕上がり易いメリットがあります。総合的にはコストメリットがありますが、硬度が過剰に高く、粘りが小さく、逆にもろいことでハンダクラックが生じるデメリットがあります。
鉛フリーはんだは、逆に融点が高いため、必要以上に温度を上昇させるとはんだの酸化しやすくなり、製品の酸化を早める原因につながります。しかし鉛フリーはんだの一番のメリットは、その名の通り鉛が入っていない点です。環境問題から、鉛の入った共晶はんだは避けられ、国内外向けのあらゆる製品で鉛フリーはんだの使用が推奨されて浸透してます。
-
はんだ付けの工程にはどのような種類がありますか?
大きなプロセスとして、表面実装のリフロー実装工程(いわゆるSMT実装) 、ソルダーリング装置やハンダ付けロボットを用いるフローハンダ工程と、人の手を介して行うマニュアルハンダ工程が、工程の代表となります。
-
どのような業界向けのプリント基板実装の実績がありますか?
産業機器が使われる業界全般でプリント基板実装の実績があります。自動車車載基板・電力メーカー基板・医療機器基板・通信機器基板・自然エネルギー向け基板・蓄電装置基板・紙幣識別基板等が最近の主力になります。
-
どのような種類のプリント基板の実装に対応していますか?
ガラス材のCEM-3 ,FR-4材質が大半をしめますが、テフロン基板・セラミック基板も稀にあります。また最近では余り出回りませんが、紙フェノール基板の実装も対応しております。
-
基板アートワーク設計からご相談したいです。
自社内アートワーク設計が可能ですが、キャパにより外部の協力を仰ぐ場合もございます。最近の傾向としては、アートワークから当社にご依頼いただくケースが主力となっております。
-
基板実装の最大可能サイズはどれくらいですか?
社内での基板実装はマシンの対応としてMサイズが主力ですが、弊社協力工場様との連携により、Lサイズ基板の実装も多くの受注実績を持っております。
-
基板実装のための部品調達は御社にお任せしても大丈夫ですか?
弊社では電子部品の調達から筐体に使用される板金・樹脂部品・ダイキャスト部品など、全て調達が可能です。特にプラスチック成形部品・FRP部品などの成形部品・ダイキャスト鋳造部品・精密機械加工品については、自社グループ内の工場から調達が可能のため、リードタイムの短縮にもつなげております。
-
基板のハーネス加工は対応可能ですか?
筐体組立・基板組立にハーネス部品は必須部品となり、長年お取引をしているハーネス加工の協力会社様が多数あります。当社の基板ハーネス部品調達の特色としては、弱電に強いハーネスメーカー様、高電圧に強いハーネスメーカー様、それぞれの得意分野に応じたハーネス調達が可能です。
-
基板の防湿処理にはどのような方法がありますか?
基板の防湿には、基板全体をシリコンやフッ素等の樹脂で覆うコーティングの手法と、ケースに基板を組み込み樹脂を流し込むポッティングの手法があります。また基板直接ではなく、筐体にゴム部品やOリングなどで封止するパッキンなどの手法もあります。
-
月にどれくらいのロット数の基板まで実装可能ですか?
基板の実装点数により左右されますが 携帯電話等に使用される基板の大ロット量産については、最大で月 20,000台超をこなす実績があります。しかしながら大ロット生産品は海外生産の傾向が益々高まっており、国内生産品のロット数は月300~1,000台程度の少量多品種生産が、最近のロット傾向の主力と変化しております。
-
基板の検査工程では、どのような検査に対応していますか?
基板生板でのフライングチェッカー、実装後のビジュアル検査からICTよる導通検査・製品状態でのファンクションテストを主体として 他にSMT工程でのBGA部品などにはX線検査を実施しております。
-
高電圧機器の基板実装をお願いしたいのですが、耐電圧試験は御社にて対応可能ですか?
電力メーカー向け製品・鉄道車載製品など多種の高電圧機器の製造を行っているため、耐電圧検査を必要とする製品には当社にて耐電圧試験を実施しております。
-
FMEAもお願いできますか?
製品及び製造プロセスにおいて故障モードを事前に洗い出し、影響を分析評価した上で対策を講じることは最も重要で、弊社では工程FMEA・設計FMEAを実施しております。
-
鉛フリー実装にも対応していますか?
弊社では 鉛フリーと共晶のどちらの実装対応が可能です。混入防止からそれぞれ別のラインで実装対応しております。
-
海外で使用する基板についても製造いただけますでしょうか?
海外で使用する基板は国際規格のIEC規格に対応した物をはじめ お客様とのお打合せに応じたUL規格・CSA規格・C-UL規格等多くの実績がありお客様のご要求に応じた対応が可能です。