ダイカストで発生する引け巣のメカニズムと対策を徹底解説!
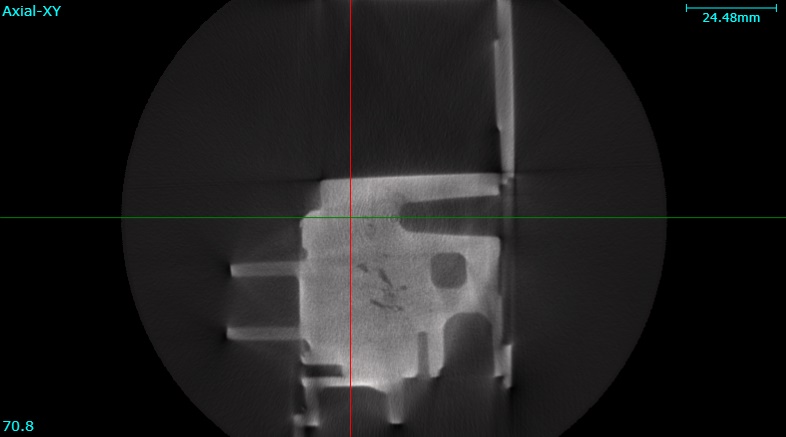
引け巣(ひけす)は、鋳物や鋳塊の製造において生じる凝固収縮欠陥孔のことです。英語では「shrinkage cavity」または「shrinkage porosity」と呼ばれます。これは、溶融金属が固体に相転移する際に、金属の凝固収縮により発生する鋳巣の一種です。
ダイカスト工程でも、高温で溶かした金属を型に流し込み、短時間で成形することで高精度な部品を大量生産できる一方で、引け巣が発生することがあります。
引け巣は、製品の強度不足や外観品質の低下を引き起こす原因となるため対策が必須のものとなります。
今回は、引け巣が発生するメカニズムと、具体的な対策方法について解説します。充填条件の最適化や冷却速度の調整、部分加圧など、実際の製造現場で有効な対策を徹底的に解説し、ダイカスト製品の品質向上に役立つ情報をお届けします。
鋳巣とは
鋳巣は、金属の鋳造過程で生じる空洞や気泡のことを指します。鋳巣には主に3つの種類があり、その種類に合わせた対策が重要となってきます。鋳巣は、製品の内部や表面に現れることがあり、見た目だけでなく強度にも影響を与えるため、品質管理上重要な問題となります。
引け巣も鋳巣の一種となります。
引け巣とは
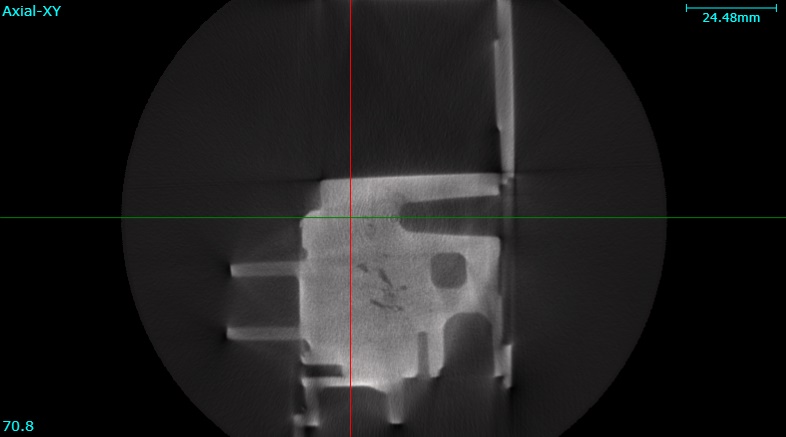
引け巣は、金属の溶湯が冷却収縮する際に内部や表面に生じる小さな凹みや空洞です。主に材料の不均一な冷却や圧力不足、型の設計不備により発生し、製品の外観や強度に影響を与えます。溶湯を冷却すると固体凝縮が進むため、凝固した分の溶湯を補うため、液体側から溶湯が補給されます。凝固によって溶湯の補給が出来なくなったタイミングで、凝固による体積の縮小分が引け巣となります。
引け巣はその生成メカニズムから、厚肉部や交差部の中心付近に発生しやすい傾向があります。また、不均一な冷却が起こる部分や、最終凝固部に集中します。
引け巣の種類
引け巣は主に以下の2種類に分類されます
内引け巣(内びけ巣)
内部ひけ巣は、鋳物の内部に生じる空洞で、一般的に「引け巣」と呼ぶ場合、この内引け巣を指すことが多いです。鋳物の内部に比較的大きな空洞が発生するのが特徴で、厚肉部や交差部の中心付近、最終凝固部に発生しやすい傾向があります。
内部ひけ巣の一種として、「ざく巣」があります。ざく巣は、アリの巣状の空洞が多数集まった複雑な形状をしているのが特徴です。
内部ひけ巣は、外部からは見えないため、発見が難しく、X線検査や超音波検査などの非破壊検査が必要となります。内部ひけ巣があると、製品の強度や気密性に悪影響を及ぼす可能性があります。
外引け巣(外びけ巣)
外引け巣は、鋳物の表面に生じるへこみのことを指します。内部の凝固収縮に影響を受けて発生し、一般的に上型面で発生しやすいです。湯圧が常時かかっている下型部には発生しにくいという特徴があります。
外側に作られる殻が強固な場合は内引け巣になりやすく、殻の一部に弱い箇所があると外引け巣になりやすいです。
外引け巣は、外観不良の原因となるだけでなく、製品の強度を低下させる可能性も孕んでいます。特に、応力が集中しやすい部分に発生した場合、破損のリスクが高まります。
これらの引け巣は、金属が液体から固体になる際の凝固収縮によって発生します。アルミニウムの場合、凝固収縮率は約6.6%にも及ぶため、適切な対策が必要となります。
引け巣は鋳物の強度低下や機能性の問題を引き起こす可能性があるため、鋳造工程において重要な課題となっています。そのため、金型設計や工程設計の最適化、押し湯の適切な配置など、様々な対策が講じられています。
引け巣のメカニズム
引け巣の発生メカニズムは、以下のような過程で進行します:
①凝固収縮の発生
金属が液体から固体に変化する際、体積が減少します。
アルミニウムの場合、凝固収縮率は約6.6%にも及びます。
②溶湯の冷却と凝固の進行
金型の外側から冷却が始まり、表面から凝固が進みます。
鋳物の内部は外側よりも遅れて凝固します。
③溶湯補給の不足
凝固が進むにつれて、液体状態の溶湯が減少していきます。
凝固の最終段階で、収縮した体積を補うための溶湯が不足します。
④空洞の形成
溶湯の補給が不十分な部分に空洞(引け巣)が形成されます。
最終凝固部に空洞が集中して発生します。
ダイカストの引け巣対策
ダイカスト製造において、引け巣の発生は製品の品質を大きく左右する問題です。ここでは、一般的な引け巣対策の手法について紹介いたします。
金型設計の最適化
金型設計は、ダイカストにおいて引け巣の発生を抑制する上で最も重要な要素の一つです。以下のポイントを考慮することで、効果的に引け巣を防ぐことができます。
- 厚肉部の解消: 厚肉部は冷却速度が遅くなり、引け巣が発生しやすいため、肉厚を均一化し、急激な温度変化を避ける設計が重要です。
- 適切なゲートの配置: 溶湯がスムーズに流れるよう、適切な位置にゲートを配置することで、引け巣の発生を予防します。
- 冷却回路の設置:金型内に冷却回路を設置して効率的に冷却することで、凝固速度を調整し、引け巣の発生を抑えます。
工程設計の最適化
鋳造工程における適切な管理も、引け巣対策に不可欠です。
- 注湯温度の管理: 溶湯の温度を適切に保つことで、凝固速度をコントロールし、引け巣の発生を抑制します。
- 金型温度の管理: 金型の温度も、凝固速度に影響を与えるため、適切な温度管理が重要です。一般に、温調器や離型剤などの外冷により型温をコントロールします。
- 金型圧力の管理: 金型内の圧力を適切に管理することで、溶湯の充填不良を防ぎ、引け巣の発生を抑制します。
フラックス処理
フラックス処理は、不純物を取り除くための化学処理です。金属の酸化を防ぎ、鋳造品の品質を向上させる効果があります。フラックス剤は通常、粉末状で使用され、成分としては塩化ナトリウムや塩化カリウムが含まれることが多いです。
フラックス処理が引け巣に与える影響は以下の通りです。
- 酸化物の除去
フラックス処理は溶融金属内部にある酸化膜を除去し、純度を保つ効果があるため、鋳造時の欠陥リスクを減少させます。酸化物が残ると、強度の低下や引け巣、その他の欠陥が発生しやすくなります。 - 脱ガス効果
フラックス処理には脱ガス効果もあります。金属内に含まれるガスが放出されることで、内部にガス孔が形成されることを防ぎます。
また、これらの引け巣対策以外にも異なる加圧法やダイカスト法による引け巣対策もございます。
局部加圧による引け巣対策
ダイカストにおける局部加圧法は、鋳造プロセス中に特定の部分を加圧することで、製品の品質を向上させる技術です。この方法は、特に引け巣などの欠陥を抑制するために用いられます。
局部加圧による引け巣対策のメカニズム
局部加圧は、金型内での凝固過程中に、一部を直接加圧して引け巣を抑え込み、空洞を少なくする製法です。この方法は、「スクイズ併用ダイカスト」「局部加圧ダイカスト法」「二段加圧」「部分加圧」などとも呼ばれています。
局部加圧法は、溶湯を金型キャビティ内に充填した後、凝固が始まる前に特定の部分をピンや油圧シリンダーで加圧することにより、凝固収縮による体積減少を補うことで、引け巣の発生を抑制します。
特に、凝固が送れる最終凝固部などに対して、加圧ピンを用いて引け巣を防止します。
局部加圧のメリット
局部加圧ダイカスト法の利点は、鋳造プロセスにおいて製品の品質を向上させるための重要な技術的メリットを提供します。以下にその主な利点を挙げます。
- 引け巣の抑制: 局部加圧により、凝固中の収縮を補うことで、引け巣の発生を効果的に抑制します。これにより、製品の内部品質が向上します。
- 製品の強度向上: 加圧によって鋳物の密度が高まり、機械的強度が向上します。これにより、耐久性の高い製品を製造することが可能になります。
- 気密性の向上: 局部加圧は、鋳物の気密性を高めるため、特に高圧や高気密が求められる部品に有効です。これにより、漏れのリスクが低減されます。
- 局所的に厚肉部を有する複雑な形状に有効: 局部加圧は、局所的に厚肉部を有する複雑な形状の鋳造においても優れた結果をもたらし、設計の自由度を高めます。
これらの利点により、局部加圧法は、高品質で信頼性の高い鋳物を製造するための重要な技術として採用されています。
OEM・EMSパートナーズ.comの引け巣対策
スクイズ併用ダイカストによる引け巣対策
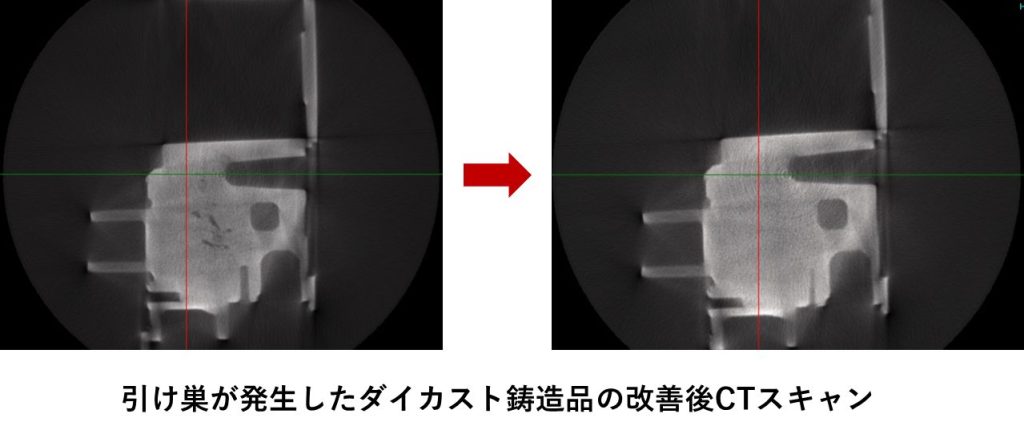
当社は局部加圧法(以下、スクイズ併用ダイカスト法とする)を採用しております。スクイズ併用ダイカスト鋳造法は、キャビティ内に充填された溶湯を加圧ピンにより直接強制的に加圧して、加圧維持したまま凝固完了させる方法です。局部的に肉厚が厚い部分のある製品の該当部分に局部加圧をすることによって引け巣を防止することが可能です。そのため、気密性が要求される製品、薄肉部分と厚肉部分が同一製品内にある製品はスクイズ併用ダイカストによる鋳造が向いております。
OEM・EMSパートナーズ.comのダイカスト製造
鋳造~検査まで 一気通貫の製造体制

当社の一番の特徴は、鋳造・加工・組付・検査までを当社のみで、一気通貫で対応できる点です。通常であれば複数の製造先に依頼をするような製品も、一気通貫で対応することで、厳しい要求品質の製品も基準をクリアして製造することが可能です。また、個別溶解炉や最新のNCマシン・マシニングセンターを有しておりますのでお客様の個別にご要望にも柔軟に対応し、お困りごとを解決いたします。
個別溶解炉による異種材対応&小ロット対応

当社は個別溶解炉を採用しております。個別溶解炉は一度に少量の材料しか溶かさないため、個別の生産に向いています。そのため異なる種類の材料を処理する際に向いており、異なる合金を組み合わせることで特性に優れる材料を作製できます。また、溶かす対象物が個別となると、熱効率が良く、プロセスの制御も容易になるため、安定した品質のダイカストが可能です。
複雑形状・多工程品の圧倒的なQCD対応

当社は、長年にわたり自動車メーカー様の厳しい要求にお応えしてきた、確かな実績と高い技術力を有しております。複雑な形状を有した製品や、数十工程にも及ぶ多工程品であっても、一気通貫対応によるQCDに優れた製造が可能です。過去には300点にも及ぶ組付品の対応実績もございます。
軽量化や工法変換といったお客様のプラスになる付加価値提案も強みとしておりますので、ご要望以上の対応を実施させていただきます
金型内製によるスピーディな立ち上げ

当社では、自社工場内で金型の設計・製作が可能です。同一工場内で金型の設計・製作から、製品の製造まで実施しておりますので、金型の改善が必要な難易度の高い製品であっても、緻密な連携によりスピーディに対応することが可能です。製造と金型両面のノウハウを活かしてお客様に最適なご提案を実施します。
ダイカスト事例
続いて、実際に当社が製造したダイカスト製品の事例をご紹介いたします。
オイルパン
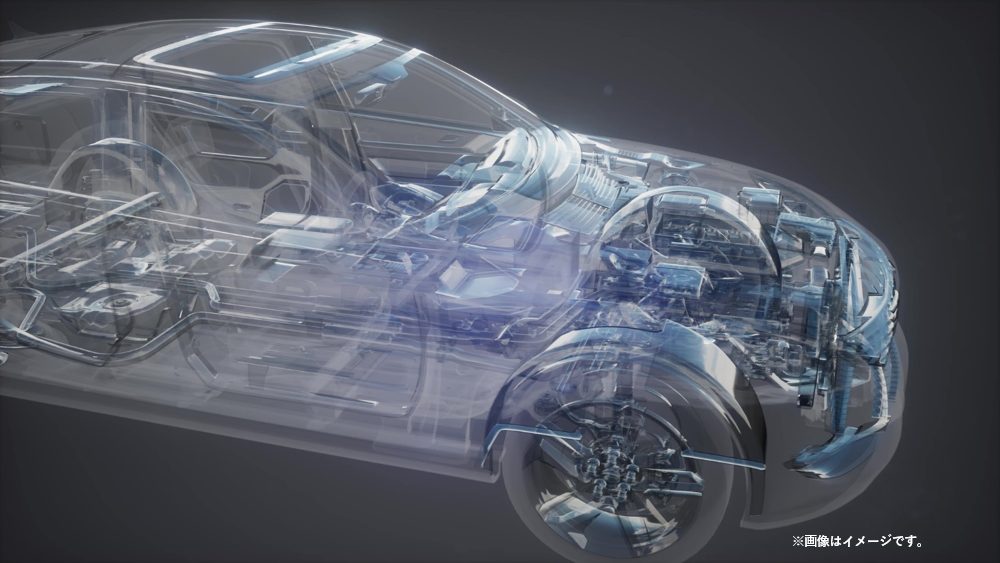
従来からお取引のあるお客様から農機具用のオイルパン部品のご相談を頂きました。
特徴としては、300 x 400 x100と比較的サイズが大きく、鋳抜き穴数が多い点が挙げられます。
ダイカスト製品の引け巣でお困りの方は、OEM・EMSパートナーズ.comまで!
当サイトを運営する日東電気グループでは、自動車部品メーカー様向けに長年製品をお納めしてきた確かな実績から、ダイカスト製品の製造実績と成形不良改善のノウハウが豊富にございます。高い技術力と、不良調査から改善まで一気通貫で対応可能な生産体制を活かしてQCDに優れたダイカスト製品の製造が可能です。
ダイカスト製品の鋳巣不良でお困りの方は、OEM・EMSパートナーズ.comまでご相談ください。
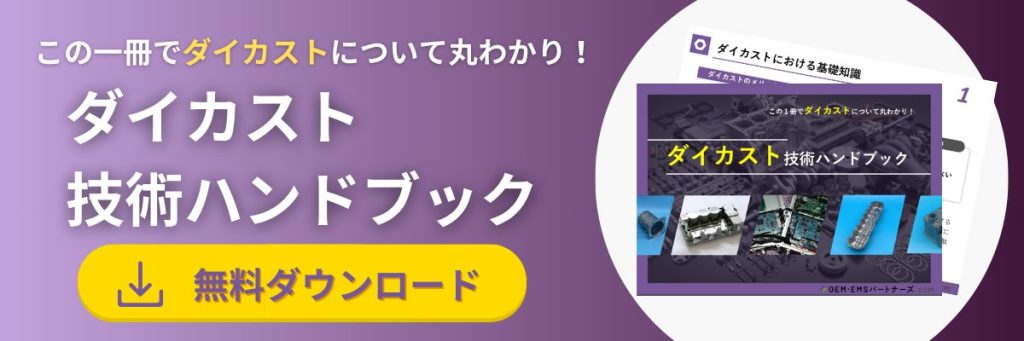
また、OEM・EMSパートナーズ.comではこの他にもダイカストについてのお役立ち情報を掲載しております。